All-Electric Trees, Subsea Separation, Smart-Well Systems Driving Subsea Production
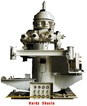
Contents
Fiber Optics
Subsea Separation
When the oil industry first ventured offshore, it took with it the same production equipment it had been using onshore for more than a half-century. Indeed, to this day christmas trees on fixed or floating production platforms hundreds of miles from shore are indistinguishable from those used in the desert or the mountains.
But when operators stepped off the continental shelves, the industry was faced with a dilemma. Control was still required at the wellhead, but extreme water depths, harsh environments, and remote areas lacking infrastructure made installation of surface facilities on which to place the controls economically and often physically impossible.
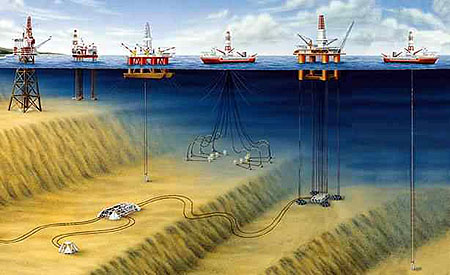
In response, the industry developed the science of subsea production through trees that could be placed on the seabed, thousands of feet below the ocean surface, and controlled from surface facilities miles away. The forerunner of the modern subsea trees appeared in the early 1980s. But falling commodity prices turned operators from such exotic developments, and it would be more than a decade before subsea trees became a common production strategy.
Besides their ability to work miles beneath the sea, and some obvious configuration differences, what really separates the subsea tree from its "dry" ancestor, is its remote functions capabilities. Valves and chokes on early subsea trees, because the distances from control to tree were relatively short, were remotely actuated through totally hydraulic systems.
But as subsea trees were set ever farther from their central control facilities, particularly in the Gulf of Mexico where those distances were quickly approaching 100 miles, the industry was forced to set aside some traditional biases against combining electronics and hydraulics. Today most deepwater wells are equipped with electrohydraulic systems.
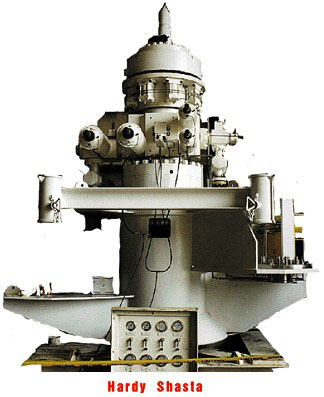
That is because, for one thing, sending an electronic signal to engage the hydraulic motor at the valve, eliminates lag time associated with sending that impulse via hydraulic pressure. For another, hydraulic lines are much heavier and thicker than electrical ones and so are impractical over great distances and depths. The improved efficiencies and extended distance capabilities of electronics also means old platforms in dying fields far from deep water gain new life as control facilities for new deepwater finds.
Lines carrying hydraulic fluid, injection chemicals, and electricity between the surface and the wellhead are bundled within a single housing, called umbilicals. Because they must be armored to survive in an extreme environment for the life of the field, as the water in which they are laid deepens, smaller and lighter is better. As such, much attention has been paid in recent years to reducing their weight and size.
An early successful strategy towards that end was multiplexing, carrying power and communication on the same line. Historically umbilicals contained a pair of electric lines for power, a pair for communication, and a pair for redundancy. Multiplexing places all the tasks on a single line from surface to subsea field from as far away as 60 miles. Then, at the seabed, the coded signal is routed to the intended wellhead actuator. Communications returning from the individual trees are likewise sorted at the surface by their individual code.
In the deep, cold waters beyond the continental shelf, water temperature at the seabed is often very close to the freezing temperature of water. Under such conditions, it is a rare well that will not produce paraffin or hydrates as it travels miles between wellhead and platform.
Flow assurance, the science of keeping lines free from such events, is critical to subsea production operators for two very expensive reasons. First, hydrates and paraffin blocks are sufficiently strong to stop all production from a field, even the high-rate, high pressure ones now being discovered in the ultra-deep waters of the US Gulf. That means a loss of tens of thousands of barrels or millions of cubic feet of production per day.
And second, once they form, removing hydrates and paraffin from deepwater flow lines is almost always extremely problematic and expensive.
Interestingly, despite the high-tech world that is subsea, the first line of defense in the war for flow assurance is the industry low-tech standby of chemical injection at the wellhead. In the first, less remote installations, each well had its own chemical injection line metered at the surface according to its unique chemical requirements. But as the water deepened and the number of remote wellheads served by a single platform grew, the lines threatened to become too large for the boats reeling them off their decks. The solution, not unlike the method for reducing electrical lines, has been a single chemical line between the facility and the field and to place meters at each wellhead to dose each well according to its specific needs.
Fiber Optics (back to top)
Like many areas of the offshore industry, fiber optics holds promise for several innovations in subsea production. More power and communications can be placed on fewer lines and it will be easier to create what many subsea tree experts have long advocated—an all-electric subsea tree.
While fiber optics must be armored the same as standard wire and therefore offers the umbilical itself no real size difference, it does offer other size advantages, particularly when used with an all-electric tree.
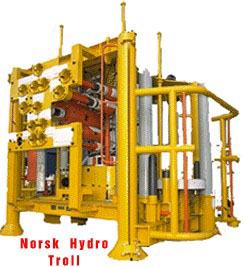
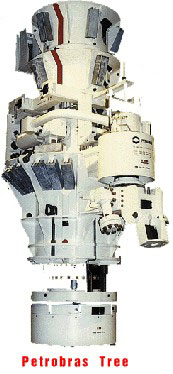
All-electric subsea trees can be made smaller, lighter, and cheaper than those forced to accommodate hydraulics, meaning their tree sections, or pods, can be more easily removed to the surface for repair using remotely operated vehicles. That, and a breakthrough connector recently developed by ABB Seatech that permits transmission of high-voltage electrical power along great distances under water, makes the eventual emergence of all-electric trees a near certainty.
Of particular interest to many engineers, is that all-electric trees lend themselves easily to smart well technology. That is because the electrical connections at the wellhead easily facilitate connection to power lines that run down hole to such devices as flow control valves and permanent downhole pressure and temperature gages.
And finally, many subsea operators expect to add fiber optics to their arsenal in the all important fight for flow assurance by installing them the length of flow lines running along the ocean floor. Because they change signal strength with pressure and temperature, fiber optic lines so arranged would serve as permanent pressure and temperature gages with readout at the surface. Changes in those two parameters pinpoint blockages at their earliest stage of formation when they can be most easily handled. Early detection also prevents production losses caused by operators' tendency to err on the side of caution and by pigging the line more often than is absolutely necessary.
Subsea Separation (back to top)
Lately, engineers at ABB Seatech have introduced a concept that will likely impact subsea production as significantly as development of the subsea tree itself: subsea separation. "What can happen is overall fluid production exceeds peak production," said ABB's John Allen. "So you have to size your flowline to be bigger than it would need to be to produce just the hydrocarbons."
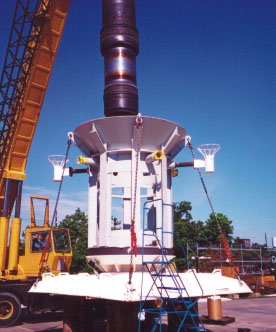
The ABB subsea separator, known as SUBSIS, is placed at the subsea wellhead where separated water can be re-injected. The first system was installed in the Norwegian Sea at the Troll Pilot Field in the first quarter of 1999 and is poised to accept production. "We are not running through the separators now," said Allen. "But they have run sufficient tests to be confident about them and we will be doing separation and re-injection through them in February or March 2000."
The economic consequences of the process, are immense and immediate as operators are able to save millions by using miles of much smaller diameter pipelines. There is also the savings in water disposal costs, including those generated by strict environmental requirements for disposed water. Too, subsea separation greatly enhances flow assurance efforts by removing almost all the water from the flowline, lessening the possibility of hydrate formation.
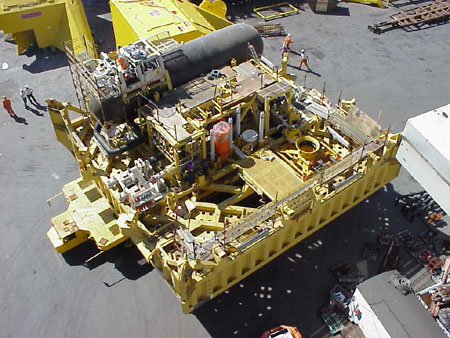
The long-reaching effect of subsea separation, however, will be its impact on reservoir management. By greatly lowering the hydrostatic head of fluid rising from ultra deep waters to the surface through the removal of heavier-than-oil water, back pressure against the reservoir is greatly reduced and depleting reservoirs will be able to produce even as their natural pressure falls off. And in some cases well life can be even further prolonged by re-injecting removed water to the producing zone to maintain formation pressure.
Because of the nature of the Gulf of Mexico and North Sea wells, particularly in the Norwegian sector, the capital expenditure for subsea separation can be deferred until well after production has begun.
"You can design your system to incorporate (SUBSIS) but you don't usually have to install it right away because normally reservoirs produce without much water at first," explained Allen. "So by designing the system to incorporate the separator later reduces capex or delays it."
Much of the future of the oil industry will be in deep and ultradeep water. The promise is high but so is the cost. It will require such innovations as all-electric trees, subsea separation, and smart-well technology to keep lifting costs at a point where the industry can be profitable even at the inevitable low-end of the commodity price cycle.