Race to develop subsea processing becoming intense
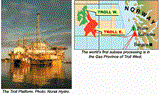
By John Howes, London
Contents
The Troll Pilot
Other subsea processing developers
At the recent Underwater Technology Conference in Bergen, Norway, Olav Indeberg of Kongsberg suggested that subsea separation was approximately 30% cheaper than processing the wellstream on a floater. With savings such as this, the battle to design and engineer workable subsea processing systems has become intense. The technology reached an important landmark earlier this year, when the Troll Pilot came on stream.
The value of subsea processing is considerable due to a number of factors. These may include reduced transportation costs, reduced back pressure, routing flexibility, production optimization, the lack of weight/stability constraints, reduced environmental impact, and enhanced recovery. It can allow existing infrastructure to be exploited yet provides a deepwater and long offset capability. In a well with a high water content, a subsea system would free up ullage in the pipelines and reduce corrosion. Many of these factors appealed to Norsk Hydro when it looked for strategies to develop its Troll oil field.
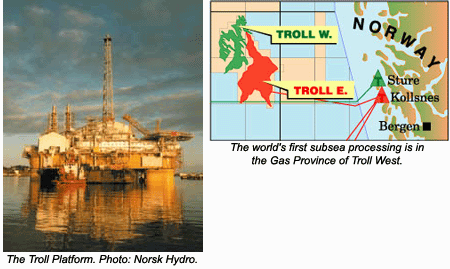
Troll lies approximately 80 km northwest of Bergen. Primarily a gas field, it still contains around one billion bbl of recoverable oil from its thin layers. It is envisaged that the production will eventually result in large amounts of water also being produced. This prompted operator Norsk Hydro to use the world's first subsea separation station called the Troll Pilot. Troll Pilot, was developed by ABB and built at the Nymos shipyard at Eydehavn, on the southwest coast of Norway. Gorm Gundersen, head of ABB's Oil, Gas, and Petrochemicals section, said the global market for subsea oil and gas processing is growing, especially in the North Sea, the Gulf of Mexico, and off the west cost of Africa. It has been put at US$ 500-600 million a year within the next few years.
At the heart of the Troll Pilot is the ABB technology called SUBSIS (SUBsea Separation and Injection System). Monitored and controlled remotely, SUBSIS separates and pumps oil-free water from the oil stream directly back into the reservoir, rather than discharging the produced water into the sea, as is done in surface systems. This means that capacity on the platform can be used for larger volumes of oil. SUBSIS also cuts the amount of chemicals needed in conventional surface systems to maintain the flow of oil, allows considerable energy savings, and is said to improve oil recovery rate as much as 50%. The Troll Pilot was installed at a depth of 350 meters by the lifting ship Maxita and brought into operation in May 2000 and afterwards on 23 June.
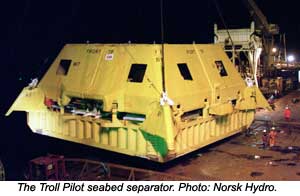
"At present, Troll Pilot is being used to separate oil and water only from two of the eight planned production wells," said a spokesman. "These two wells do not produce the requisite amount of water to justify the Toll pilot's constant use, however the third well will come onstream in October, whereupon the Troll Pilot can be used continuously." The Troll Pilot will be able to handle 63,000 bbl of liquid and 800,000 cubic meters of gas. This is the first time such technology has been used anywhere in the world.
Other subsea processing developers(Back to Top)
Another company active in seabed processing over the last 15 years is Kvaerner. Early work was based around its NOK120 million Kvaerner Booster project, however the company has since developed a Modular Subsea Processing System (MSPS). This consists of an array of units that can be configured for specific field requirements.
Kavaerner is currently concentrating on the multiphase pump, compact seabed coalescer, separation systems, and control modules. This work is funded under Demo 2000 or in collaboration with Norsk Hydro.
FMC Kongsberg has also developed a modular system called the Host, however, in recent years, it has been developing its subsea production architecture in an alliance with Aker Maritime.
Aker Maritime's seabed production activities commenced with work on the Statfjord Nord subsea bulk water removal project, but more recently, has been carrying out the Sogn Subsea Processing Study jointly with Kongsberg Offshore, which is looking at hydrate prevention philisophy, power distribution, and subsea equipment technology screening.
Not only does a subsea production system require a number of technologies such as single- and multiphase pumps, compressors, high efficiency separators, wellstream desanders, and instrumentation packages, it also requires considerable thought into the overall subsea system design and layout arrangement, subsea electrical power distribution, control system topology, oil in water monitoring and process control valve selection.
The similarity between these three systems is that they were all developed in Norway, which has grown over recent years to be the seabed processing capital of the world. This commitment has been driven at a high level by the innovative Demo 2000 demonstration program. This venture started its life as the industry was reeling from the low oil prices of 1998. The Ministry of Petroleum & Energy asked companies to predict the technology necessary to satisfy the next generation of offshore projects. It then contributed NOK100 million towards this research to increase the speed of the development and be sure Norwegian companies were spearheading the technology.
In his keynote address to the UTC, Jostein Dahl Karlsen of the Ministry of Petroleum and Energy recognized the need of getting the technology to the marketplace as quickly as possible. "Only by proving the Norwegian technology at home," he said "can companies be confident in taking the equipment and concepts to other areas."
Also speaking at the conference, Oddgeir Johansen of Elf Norge suggested that the Demo 2000 program might look at the area of long distance production directly to shore.
One interesting point made by Johansen when considering subsea separation, was that for gas production, the reduction of water in the pipeline to 1% would obviate risk to hydrate formation. In an oil development, however, the water has a higher heat retention than crude oil. The removal of too much water would result in a cooler wellstream and therefore increase the possibility of wax deposition.