Pentair Oil & Gas Separations
4301 West Davis
Conroe, TX 77304 US
936-788-1000
Conroe, TX 77304 US
936-788-1000
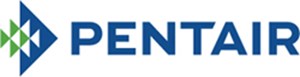
Company Overview
Pentair Oil & Gas Separations leads the way in the design and manufacture of advanced technologies for the separation of liquids, solids and gases.
This website uses cookies to ensure you get the best experience on our website. Learn more