Anadarko's Hickory Platform Fasttracked Via Paragon Engineering & Design
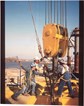
Hickman Brown, Paragon's project manager, says the PDMS system has minimized design conflicts and interference between structural, piping, electrical/ instrumentation, and other components.
Mike McEvilly, Anadarko's project manager for Hickory, echoes industry enthusiasm that PDMS technology holds a lot of promise for the offshore arena.
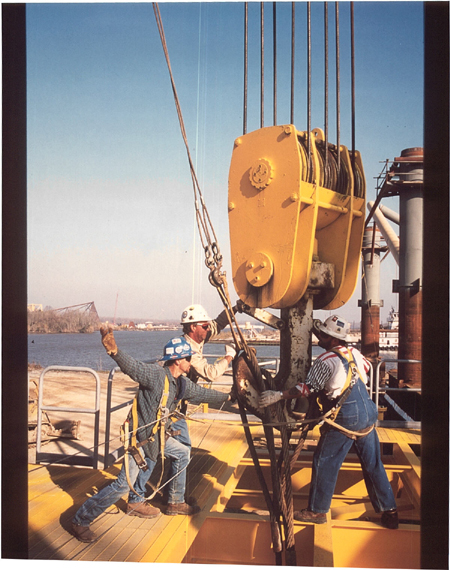
"From a conceptual viewpoint, the ability to walk-through a facility using a 3D model presents a number of industry benefits, including early resolution of design clashes and improved safety through better anticipation of hazards and early training of operations personnel," said McEvilly.
McEvilly adds, however, that Hickory is in the early stages of piping installation, making a reality check necessary as the project progresses.
"We really won't know the extent of our success in using PDMS until we begin hanging the majority of the pipe on the deck, but my inclination is that this technology is going to be a plus as an industry application," he said.
Brown says that a PDMS project requires a different project approach, with a lot more up-front engineering and design effort required before creating a 3D computer model.
"To build a 3D model of a facility, we must first build a complete data base of equipment information, including valves, flanges, pipe, fittings, vessels, skids, etc. The data base ultimately holds the characteristics and properties, including physical dimensions, weights, sizes and wall thickness, of all facilities equipment," said Brown.
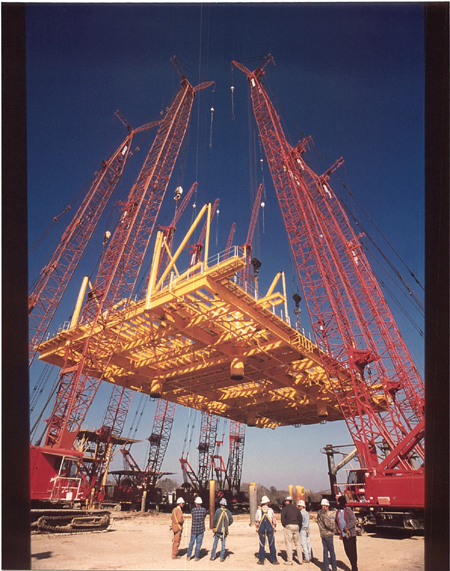
He added that to build an effective computer model, engineering concepts need to be closer to 70-80% completed versus about 40% completed before standard 2D drafting commences. Advancing engineering design prior to beginning a 3D modeling effort yields overall drafting efficiency gains versus the traditional 2D drafted project. The efficiency comes from the ability to make real-time solutions to design problems, which are readily identified in the 3D world, as opposed to the cyclic nature of creating, checking, and correcting 2D plans and sections.
"The process of building a computer model, versus a traditional 2D plot plan, helps create a better-engineered product, requiring greater consideration of all components and their interface before producing any drawings," said Brown.
The 3D data base model has the added benefit of automatically generating piping isometric drawings and material lists.
In addition to the challenges associated with implementing new technology, the Hickory project, says Brown, is schedule-driven to complete in parallel with a similar Gulf of Mexico project for Anadarko. This strategy has facilitated use of available yard space while permitting scheduling of either Heerema's heavy-lift barge SSCV Balder or its SSCV Hermod to install the platforms back-to-back. The first installation scheduled is Anadarko's Tanzanite platform, presently in fabrication at Aker Gulf Marine in Ingleside, Texas. The Tanzanite platform is scheduled for installation on Eugene Island Block 346 in early August. Hickory, destined for Grand Isle Block II 6, will follow with loadout from Gulf Island Fabrication in Houma, Louisiana. Both the Hickory and Tanzanite platforms include four-legged jackets designed for 324 ft and 315 ft of water, respectively. The Hickory and Tanzanite decks will each weigh approximately 3,500 tons and 4,000 tons, respectively.
To make the concurrent projects a success, McEvilly, who leads Anadarko's core management team for both Hickory and Tanzanite, says Anadarko has encouraged a lot of commonality in terms of equipment used, process configuration, piping, and instrumentation/electrical systems applied.
"We've worked hard to achieve a consistent design and operating philosophy for both platforms. Our design firms and fabrication contractors have worked well together to ensure that happens," said McEvilly.
Both platforms are being designed to include programmable logic controllers, rather than pneumatic air systems. This technology, while not new to the industry, represents a relatively new offshore system for Anadarko operations. Consistent design applications for both facilities will lend flexibility in transferring operations personnel between the two platforms, adds McEvilly.
In an effort to support the aggressive project, Paragon has worked very closely with Anadarko in expediting purchase orders and tracking equipment. The concurrent projects, valued at approximately US$100 million, have provided economies of scale with common types of equipment being ordered. In fact, valves, utility equipment, safety equipment, and other common supplies have been ordered together.
McEvilly adds, "We've put a lot of faith into Paragon and each of the contractors and the efforts are paying off. Both projects are on schedule and we're looking forward to production start-up later this year."
Production equipment on the Hickory platform is sized for 300 million cf/d of gas, 15,000 b/d of condensate and 20,000 b/d water. Tanzanite will produce oil, but production rates are not available at this time.