Automation, High-Tech Characterize Next Generation of Drilling Rigs
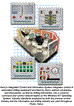
by John Murphy, Houston
The technological changes that have swept through the upstream sector of the oil and gas industry during the 1990s are nowhere more evident than on the drilling rig floor. Once the dominion of men who labored at no small personal risk to wrestle heavy, dirty iron, guided only by rudimentary gages, the gritty soul of the drilling operation is quickly being transformed into an automated high-tech showplace.
This revolution is being carried out simultaneously on the related fronts of automation and telecommunications. Remotely operated pipe handling machines and iron roughnecks capable of lifting and maneuvering pipe with only remote human intervention are automating basic, brute-force rig operations. And as a consequence, operations are safer, more reliable, and ultimately quicker and more cost efficient.
At the same time, computerization of rig sensors and instruments linked to telecommunications is making ages-old drilling measurements like weight on bit and rotary speed available in real time to petroleum professionals around the globe. Likewise, these and a host of other parameters are now being gathered, analyzed, stored, and ultimately manipulated with an eye towards even more automation.
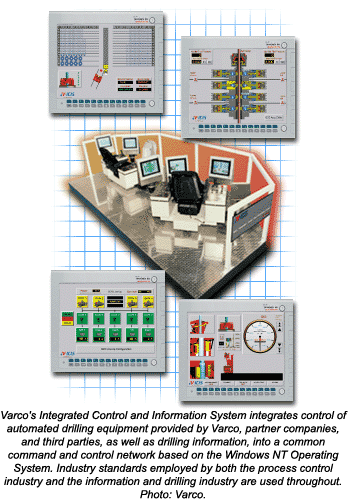
"Contractors now are putting satellites [dishes] on the rig and tying that instrumentation into the guy in the office who can look at exactly what is happening on the rig in real time," said Terry Tavin of MD Totco, a division of Varco, the drilling equipment manufacturer that introduced the top drive drilling system in the early 1990s that has become a staple of modern rig specifications. "It is really taking the rig instrumentation, the basic parameters they use, and doing a better job of drilling."
Doing a better job of drilling generally means a faster job, since the less time it takes to reach total depth and get the rig away, the lower the costs. In deepwater scenarios that can easily translate to savings of $250,000 per day.
But it also means a better finished product. And as modern operators are discovering, that can be best accomplished by a well informed team rather than through traditional unilateral decision making by a single drilling engineer. The availability of real-time data at remote sites miles from the rig, says Tavin, makes timely team decision-making possible.
"The geologists in the office, for instance, can be looking at [well parameters] like rates of penetration and helping engineers make decisions on things like where to set casing points or to get the best cement job possible," he said. "Or if they are having a problem with the well, if there is a kick or lost circulation they can get people online to look at the data and see what is actually happening and make recommendations to solve problems with the wellbore sooner. The guy on the rig is not out there all alone anymore."
But such innovations are likely only the beginning. Just as downhole tools are now entering a smart phase in which they analyze the data they gather in order to make some logical decisions on their own in a closed-loop logic, so the drilling rig of the future may use its data gathering ability to drill substantial sections of a hole without any human intervention.
"I think we are moving into an era of smart controls," Tavin said. "We are going to have an electronic driller that is taking the real time data from sensors and allowing the rig to drill wells faster or more controlled."
That faster is not always the best way to drill a well makes what might be called smart-sensor drilling all the more attractive. Capable of making decisions at the speed of a computer, automation could well do a better job keeping a straight hole or protecting the formation being drilled than humans can because a computer can correlate and act on data more quickly and accurately. Many oil and gas wells today are under-performing because data was misinterpreted or not acted upon quickly enough.
"We are moving from just displaying data to actually using that information from those sensors that monitor the drilling parameters," Tavin said. "We are moving to applying those [sensor readings] to control algorithms that actually take over and control the drilling functions."
Depending on the nature of the area to be drilled or the order of importance of drilling parameters, an electronic driller would be programmed to act based on any set of sensors. For instance, if controlled drilling is required, that is using slower than possible rates of penetration in order to keep on track, the programmer may choose to control how fast drill line is paid out. Or it may be that speed is all and it will be the automated drillers job to see to it that some constant weight is kept on bit.
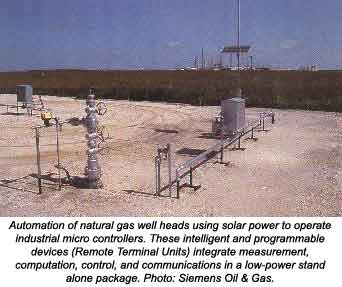
Naturally, such a complex system will hardly be limited to a single drilling parameter. While drilling with a mud motor, for instance, the operator may wish to control pump pressure to maintain a target differential pressure across the drill motor. But then, parameters such as weight on bit or rotary speed may be added as a secondary control in case conditions change in such a way as to render the primary control irrelevant.
While full automation may be in the future, it is not the distant future. Indeed, high-tech sensor and communication packages are now a reality on almost all new builds and many upgrades. And while they have been sired primarily by the industry's foray into deep water, automation is by no means confined to that arena.
"It is going on now," said Tavin. "It all kind of got started in the last round of building deepwater offshore rigs and now the whole level of controls on the rigs is beginning to be upgraded, even on land rigs."
Reportedly, giant land drilling contractor Helmrich & Payne is including the new generation of controls and sensors on new rigs to be delivered in October.
There are major physical differences between the old and new controls and sensors. The traditional oversized brake handle drillers have leaned on for generations to control pipe movement, for instance, has been replaced on the latest rigs by a joystick like those made popular by computer games. And rather than gages with large clock-type faces, large numbers and a large black needle, the driller of today will look at computer screens to get the same data and use touch screen panels instead to change everything from brake line tension to pump rates.
In a tradition-bound industry like drilling, such basic changes do not come easy. Ironically, it may be the cyclical nature of the industry that takes the sting out of the transition from old ways to new.
"Over the past five-to-seven years the level of those guys on the rigs has changed," Tarvin said. "Today they are more able and more willing to accept computerized stuff. And the drillers that started their careers in the last industry boom, in the late 70s and early 80s, are getting out and retiring now. So you have a new generation [of worker] on the rigs."
Too, during nearly 20 years of sluggish drilling activity, few new rigs were added to the fleet. That means today's rigs are aging and must be upgraded or scrapped soon. Either way, given the success operators are reporting from high-tech rigs, it is a certainty high-tech drill floors will only proliferate.
"The performance they are getting, the better texture of formation and quicker drilling time is really adding to the demand for performance class rigs," Tarvin said. "Many of the next generation rig - land and offshore – will rely on computerization."
Rig builders estimate the new generation systems cost about three times that of a conventional instrumentation and controls but the prices are easily justified by improved performance. Judging by the systems currently joining the market, operators and contractors appear to agree.