Combating deepwater hydrate formation critical as production goes deeper

By John Murphy, Houston
Each new discovery in waters beyond the familiar and well worked continental shelf required considerable investment in infrastructure before it could be exploited. As a result, development was restricted to only the most prolific fields. Whereas historically, production from profitable wells in shallow waters is often measured in hundreds of b/d of oil equivalent, beyond about 1,000-ft water depths, wells testing at less than several thousands b/d are rarely completed.
While high rates have made production from deepwater fields financially feasible, they are inevitably accompanied by high pressure and some amount of produced water creating a classic environment for hydrate formation. And deepwater production exacerbates the situation as well fluids must flow long distances through pipelines laid through near-freezing seawater along the ocean bottom.
Additionally just as higher production rates increase the likelihood of hydrate formation, they also mean greater financial losses any time that flow is interrupted. Deeper water also means removing hydrate plugs once they are formed is vastly more expensive, particularly should they become sufficiently fixed as to require intervention from special deepwater vessels or remotely operated vehicles to remove them.
The science of combating hydrate (and paraffin) blockages is known in the upstream industry as "flow assurance" and as the stakes rise with water depths, so does the pressure on industry to find a real solution to the problem. "Hydrates are a nightmare in the deep and ultradeep water [industry]," Jean-Francois Giannesini of the Institut Francais du Petrole recently told an audience of deepwater specialists gathered to discuss the technological future of their industry. "And flow assurance is cash assurance."
So important has the quest become that nearly every industry group dedicated to the deepwater technology includes a flow assurance study group. Among these organizations is the American-based DeepStar consortium, founded in the mid-1990s and comprised of dozens of operators and service companies from the world over. Both Procap 2000 and Procap 3000, multiyear and multimillion dollar programs run consecutively by Brazil state oil company Petrobras's research arm CENPES, have dedicated considerable time and personnel to flow assurance issues. Oilfield service giant, Halliburton Energy Services, recently hosted a two-day forum for scientists, engineers and clients dedicated solely to the topic.
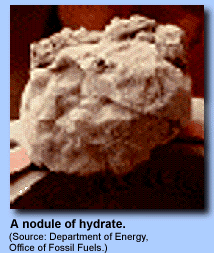
The problem is under attack on both the mechanical and chemical fronts. flowline, limited for now to circulating heated fluids through a pipeline annulus has also seen some success but is again limited by distance since circulated fluids, like the well fluids themselves, eventually lose their heat and become ineffective over some distance.
More promising are attempts to heat the flow line directly by sending an electrical current through its length. Still in early development, the process is confined to flexible pipe that, since it is comprised of composite and steel fibers, will act as a resistor converting induced electricity to heat. "I think resistance is more desirable [than circulating fluid]," said one flexible pipe manufacturer. "When you use electricity the heating will be more uniform. That is how resistors work."
Though owing to their composition it is a relatively simple matter to create an electrical current through flexible flow lines, it is costly and not overly practical since it would require a large generator be placed on a platform where space is a premium. The generator would then have to be continually fueled and even in locations where well gas is often used to run small power plants, operators would be certainly be loathe to divert such amount of natural gas from its sale line to a generator.
Chemically, the upstream industry has long pumped relatively large volumes of refined hydrocarbons, typically methanol or glycol, into the flow stream at the wellhead. The effect is to lower the temperature – known as the thermodynamic hydrate formation temperature – to which the flow stream must drop before hydrate deposition begins. The approach works well for smaller projects, particularly on land where the pump can be easily situated and maintained and in shallow waters where distances between wellhead and host platform are relatively short.
But the massive, remote projects that characterize deepwater developments create a number of problems for this approach. Primarily, as the production rates and the pipeline sizes increase, the amount of chemical necessary escalates in cost from nominal to one capable of reshaping the project's economics. Also, should the line be shut in for any length of time, traditional hydrocarbon-based inhibitors cease working and hydrates soon form. Finally, particularly in the case of methanol, the total hydrocarbon content of the well fluids can exceed allowable water discharge limits in many regulated offshore areas of the world.
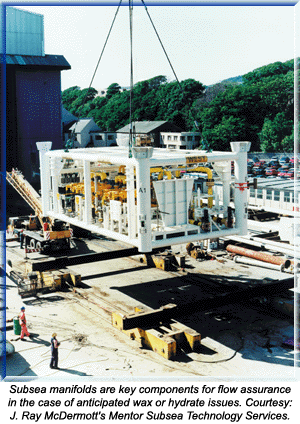
Methanol and glycol are even less efficient once a hydrate has formed and so have little use in remediation. In Brazil, Petrobras scientists have licensed a vendor to distribute a rather simple hydrate buster the company created during its Procap 2000 campaign. Once the hydrate [or asphaltine] block has been detected, two chemicals are sent independently to the site of the blockage.
"It is a really quite simple," said Marcos Assyag, Petrobras R&D program director for Procap 3000. "The two chemicals are time-released and set to react with each other once they reach the blockage. They react and create a salt during an exothermic reaction and the heat generated by that melts the hydrate."
But promise of a more robust chemistry-based solution likely will come from compounds known as "kinetic hydrate inhibitors". Water-soluble and non-toxic, KHIs are polymers that inhibit formation in pipelines, according to ExxonMobil Production Research Company scientists, L.D. Talley and G.F. Mitchell, in a paper presented at a the 1999 Offshore Technology Conference, "at much lower dose rates than methanol or glycol by greatly slowing the rate of hydrate crystal formation."
The key to KHIs, say the two scientists, is that unlike glycol or methanol they do not change the thermodynamic hydrate formation temperature. That means that even as a KHI-treated line operates under conditions favorable for hydrate formation, the process is delayed and in the case of shut-in operators still have time to resume flow before a blockage forms."
"[Using KHI] the formation of hydrate crystals is delayed much longer than the residence time of fluids in the flowline," wrote Talley and Mitchell. "If a line treated with KHI is shut-in and held at hydrate-forming conditions, it remains hydrate-free for hours, days or weeks depending on the subcooling and the KHI concentrate in the flowline."
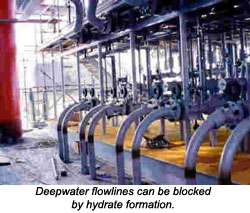
Mechanical answers to hydrates have been almost totally a matter of remediation in the form of pigging. Subsea production pipelines are built as loops and pigs, formable plastic and steel mandrels designed to scrape the pipeline wall free of deposits, are sent along them at regular intervals. This approach, while effective has several serious drawbacks. In the early days of the Campos Basin off Brazil, for instance, a poor understanding of when pigging would be required led to several instances when pigs landed in the forming blockage and only added to the problem. Sending the pig more often to eliminate the possibility the hydrate had grown too large meant considerable loss of production.
Those early near-disasters led Petrobras and others to seek methods for predicting hydrates so that pigging could be done with a minimum of lost production. Arising from this research has been several technologies, the most promising of which is the use of fiber optic cables wrapped around pipelines, to detect hydrates in their earliest stages.
Since fiber optics expand and contract with temperature, when a hydrate begins to form and long before flow pressure or volumes can be detected, the temperature of the pipe drops shrinking the conductive area of the line. That reduction in turn causes a drop in current passing along the line. And since the current can be monitored infinitely on any spot along the line, it is possible to pinpoint the exact location of the hydrate. In that way operators can optimize their operations, sending the pig neither too late to be effective nor so frequently as to cause undue production down time.
But the mechanical approach to hydrate prevention rather than remediation quickly gaining oil industry attention stems from work done for a completely different reason. In 1996 in the North Sea, ABB installed a subsea separator designed to remove produced water from the production fluids at the seabed and re-inject it down the well. It is called SUBSIS and its goal was to reduce the costs and space requirements associated with produced water. But today operators are looking at seabed water removal as a possible flow assurance tool. After all, in the absence of water, hydrates cannot form. ABB reports its system has been operating successfully since its installation.
Flow assurance has been the subject of intense research since the early 1990s and yet relatively little headway has been made toward the elimination of hydrate-induced blockage in extreme environments. Beginning in 2000, for instance, DeepStar was still instigating new flow assurance studies. Its latest a three-year, $3.2 million test loop constructed in cooperation with the US Department of Energy at the Rocky Mountain Oilfield Test Center in Wyoming.
But deepwater production is an increasingly large share of major operator's overall production as well as their capital and operating expense outlay. As the dollars spent and made in extreme water depths reach towards the billions of dollars per year, flow assurance and the technology to defeat hydrate formation will become increasingly important. With such motivation, it is likely the extremely serious problem of hydrates now plaguing the offshore production industry will soon be little more than an easily managed nuisance.