Drilling Software Enhances Operator Performance Before, During, and After Drilling Operations
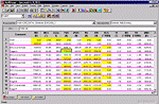
By John Murphy
Contents
Planning & Monitoring Tool
PowerPlan
In the late 1970s, engineering students were amazing one another with programmable calculators in which they could write, among other things, programs to calculate casing designs. It can be argued that these SPE-based calculations qualify as the first drilling software. But since experienced drilling engineers got the same results with pencil and paper nearly as quickly, often more accurately, and without the bother of writing programs, they remained mainly a curiosity.
The first real drilling software packages came with the growth of computer usage in general. They were designed as a way for engineers to adjust basic, interdependent well planning parameters such as mud properties, weight on bit, bit type, rock properties, and hydraulics to determine how it changed the overall drilling scenario quickly. It required a lot of input, and the result, after any number of iterations, was a well design with the theoretically most efficient casing points, hole cleaning hydraulics and rates of penetration and little else.
Engineers of the time, accustomed to doing such things by hand, were skeptical of the efficacy of these early planning tools because though they used long-proven methods of calculation, they relied on suspect input data. For instance, the earliest drilling program allowed engineers to describe an entire section's rock properties using one of three numbers representing general rock hardness. Those early programs also limited bottom-hole-assembly profile description and assumed gage holes, all of which led to questionable conclusions about such important drilling parameters as effective circulating density (ECD), pump settings, and annular velocities.
Still, as the input was tweaked by experience and as the industry moved into remote areas and further offshore where the price of failure was inordinately high and offset data minimal, it became routine to test drilling plans against computer models. Moreover, efficiencies did improve while failure rates fell as some traditional practices were shown to be overly conservative, under appreciated, or just poorly understood.
With the increasing acceptance of the computer as a drilling tool, came increasingly sophisticated software. Among the most important contributions then came from standardization through the use of API- and ISO-based calculations as well as expanded choices from data bases easily updated with the latest specialty threads, tubulars, and fluids.
Eventually databases included frequently updated prices allowing engineers to make decisions based on good economics as well as physics. For instance, it may turn out that a conservative casing string could also be economical because of availability, transportation costs, or other market forces.
Too, with increasing sophistication came the ability to consider factors in drilling that earlier, because they were too difficult to model accurately, were essentially covered by unnecessarily large safety factors that led to overly conservative and expensive well materials. The effects of temperature on drilling fluids and tubular strength, for instance, has long been fairly well described, but in other than extreme circumstances they were rarely specifically calculated. Again a too-large safety factor was invoked in order to err on the side of caution.
Planning & Monitoring Tool (back to top)
With the proliferation of real-time drilling data acquisition tools and the spread of personal computers, drilling software has evolved from essentially a planning tool to a planning and monitoring tool. By accessing such real-time data as drill bit face and logging data, and comparing that to the planned well path, operators can tell instantly where they are in relation to the target and make the necessary changes.
Also, the data uncovered during one drilling operation and the changes it engendered in the well plan can be carried over to the next well instantly, eliminating the need for redundant research or labor- and time-intensive data input operations.
When seismic data is added to the mix, operators can often do quite accurately what until now has been impossible—see ahead of the bit. That is, by using the LWD data to locate the bit on a 3D seismic plot, drillers and geophysicists know what geology awaits them in the next few feet. In the very near future, it is expected near bit sensors will actually read, interpret, and chart the formation ahead in real-time in much the same way as is now done in logging-while-drilling.
As important as real time data gathering was to bringing drilling software to the next level, the revolution in communications that has taken place just in the last decade may be even more so. Today, drilling hands on the rig and service and operator engineers and geophysicists in the office are seeing the same data at the same time. They are also able to take their particular contribution to the scenario, be it a well design or a 3D seismic map with targets and faults, and compare it to what is actually taking place half a world away.
Such service giants as Schlumberger, Halliburton, Baker, and Weatherford are already able to provide this data in fact to any PC anywhere in the world. But, Halliburton is taking it one step farther. In the next few years, they will open three data centers in various strategic locations around the globe that can be connected via satellite to any number of well jobs simultaneously from anywhere in the world. Not only will visitors to these command hubs be able to monitor the jobs but also make changes to them as quickly and directly as their representatives on location. In essence, an operator can have its top expert in any field on every job it is doing. Jobs as far away as Africa have already been so monitored in real-time from Houston.
Today's drilling software far outstrips the well planning tools of just five years ago. It allows engineers to tap vast resources of data from many similar well histories and to look at the latest data gathered in the nearest offsets. It taps the resources of seismic by comparing what the real-time sensors are seeing to what is predicted and provides safety monitoring by noting the onset of kicks and other well control events more quickly than is humanly possible. It does the hundreds of time-consuming drilling calculations that are the bane of a drilling engineer's existence, monitors bit wear, torque, and stick-slip.
And when it is all over, the modern drilling software package can perform the highly useful but onerous task of summarizing the well. Operators and drilling contractors alike are using this ability to scrutinize every rig operation down to its smallest increment to shrink non-productive rig time. They use it to document drilling trends for comparison with other wells in its database.
The ability of drilling software to enhance operator performance before, during, and after drilling operations makes it one of the most powerful tools in lowering finding costs—the industry's first line of defense against the vagaries of oil price cycles.
Schlumberger GeoQuest's PowerPlan is a prime example of an integrated drilling software system.
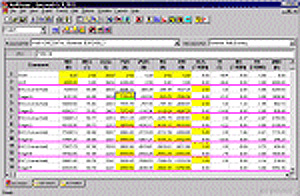
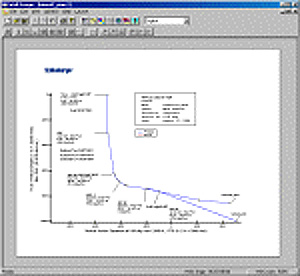
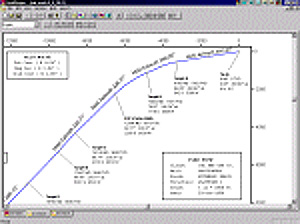
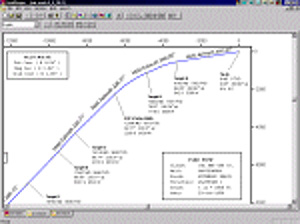
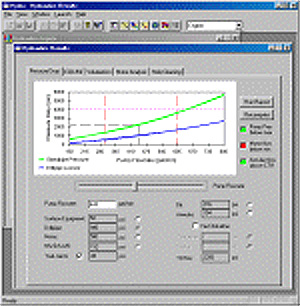
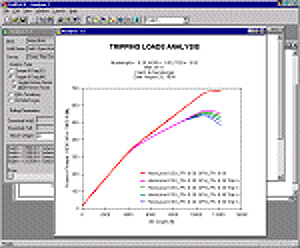
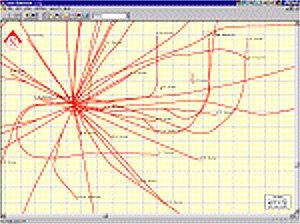
Courtesy Schlumberger GeoQuest.