Flexible Pipe Facilitates Deepwater Production, Flow Assurance
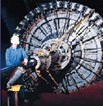
By John Murphy
Among offshore oil and gas professionals, the closing years of the 20th century will undoubtedly be remembered as the moment the industry left the safety of the world's continental shelves for the unknowns of deep and ultradeep water exploration. And just as past explorers slugged through unmapped territory adapting to it as they went, so have modern petroleum engineers had to adjust their methods to deal with an environment in which traditional methods and tools are woefully inadequate.
Before heading into deep water, few drilling or production engineers, for instance, had ever included the effects of water temperature or pressure or facility movement in their well designs. Instead they were bound to the traditional design parameters of depth, formation pressure, and fluid weights that have become hopelessly inadequate for wells drilled beneath more than a mile of ocean.
That is because so much of what was standard practice near the beach is not feasible beyond the horizon. There, piled platforms located directly above producing wells must be replaced by distant facilities located in shallower waters or floating production facilities whose heave and roll can be considerable even in calm weather. And most deepwater production must travel many miles along the ocean floor through near-freezing water before reaching surface facilities.

Likewise, in thousands of feet of water, complex subsea christmas trees, placed on the ocean floor and remotely actuated through extensive electrohydraulic systems from miles away, replace the simple surface valves and chokes of shallow water and land-based operations.
Among those technologies made impractical by this new frontier is traditional, rigid oilfield tubulars for production flow lines. Instead, the industry has turned to flexible flow lines that can easily follow the contours of the ocean floor over long distances from deepwater fields to shallow-water processing facilities.
Not that deepwater created the technology. The first offshore flexible flow line was installed in 1974, well before the industry stepped into what is now considered deep waters, for Mobil in the North Sea, by Paris-based Coflexip (now Stena Coflexip Offshore - SCO), still the dominant oilfield flexible pipe manufacturer and supplier. Two years later, the same company installed the first production riser for Petrobras offshore Brazil.
Risers are the final section of pipe that leads from the essentially horizontal flow line on the ocean floor to the deck of the production facilities and are of special interest for flexible pipe applications when those decks are on floaters. Floaters are anchored by miles-long mooring lines or held in place by computer-directed thrusters in a system known as dynamic positioning and are kept in constant motion by the heave and roll of the seas. Such motion presents obvious problems for connections made with rigid risers that are best addressed by flexible pipe.
That is because, as would of course be assumed from its name, flexibility is what distinguishes flexible pipe. SCO literature claims its 8-in. internal-diameter-pipe, for instance, can bend to a 6-ft or less radius. Because of this ability to bend without degradation of pressure or strength characteristics, flexible pipe has been a driving force behind the proliferation of floating production vessels, particularly the newly popular floating production, storage, and offloading (FPSO) vessels.
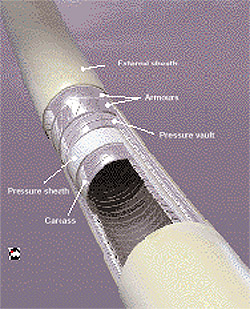
Flexible pipe derives many its characteristics from its layered constructionSCO reports its most complex flexible to date had 19 layerscentered round a layer of wound steel wires for strength and a thermoplastic barrier to prevent leaks. The system can be built-for-purpose because while the layers are designed to work together, they are also modular, meaning they can be adjusted independently. For instance, changes to the plastic lining for different pressure ratings can be made without compromising the integrity of the steel windings, themselves designed to specific strength and weight requirements.
Flexible pipe also is perfect for bundling, the practice of placing numerous lines with different functions within the protective steel and plastic coating of a single lineoften referred to as an umbilical. One strong attraction of the technique is the production line and the various control lines to be run between a surface facility and subsea tree can be laid in a single operation. And, because flexible lines are deployed from a giant aft-deck reel with connections made ahead of time, the actual pipelay operation can be done considerably faster and more safely than with traditional rigid flow lines.
Included in these bundles, beside the conduit for oil and gas, are lines that transport hydraulic fluid for valve actuation and electric cables for communication and monitoring. These bundles are also the industry's best hope for flow assurance through deep and ultradeep waters.
Flow assurance deals with hydrates and paraffin that can be precipitated out of solution by the sudden cooling of the flow stream as it travels along the ocean floor. These can and do form blockages sufficient to restrict or even stop flow and at such depths and along such distances, removing paraffin or hydrate blockages is problematic and expensive. This is especially true in deep and ultradeep fields that tend to produce at very high rates so that a few days of lost production can represent considerable cash flow losses.
Flow assurance efforts today are driven by the adage that an ounce of prevention is worth a pound of cure. As such the industry has dealt with the problem fairly successfully through the injection of chemicals that repress paraffin and hydrate formation, insulation to keep the flow stream temperature above that at which blockages begin to form, and periodic pigging to clean the pipe of any nascent paraffin or hydrates.
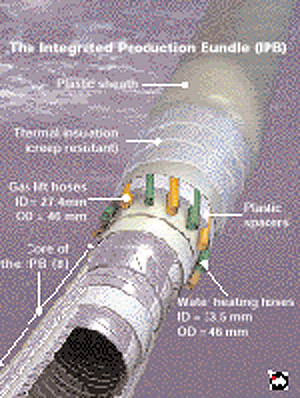
Flexible pipe is well adapted to all these methods. But it is especially well suited to invoke use of another promising technologyfiber optics. By wrapping the flow line in fiber optic lines, the line can be monitored for changes in pressure or temperature that would pinpoint the rate and location of a hydrate or paraffin build-up.
Catching it early offers the advantage of easy removal. But, more importantly, it can save operators a great deal of money as they would need only shut down production for pigging when they were sure it was necessary rather than at regular intervals that, from a desire to err on the side of caution, may be more often than necessary.
As production from ultradeep water comes nearer a reality, flexible pipe manufacturers are working on a number of creative flow assurance solutions, including more efficient insulation and circulating heated water around the flow lines to aid in fluid temperature maintenance.
More immediately, manufacturers and operators are working on stronger pipe to handle the crush of 10,000-ft waters and the ability to handle high-pressure, high-temperature gas wells. In 1997, the deepest flow line was laid off the coast of Brazil at Petrobras' Marlim Field in more than 5,000-ft waters. In the same field, the world's longest flexible riser reached from the ocean floor to a height of more than 4,000 ft.
Such feats have been made possible by accomplishing such daunting multiple tasks as creating stronger pipe to resist increasing collapse and burst pressures at greater depths while at the same time developing a lighter steel to avoid creating excessive tensile loads on the riser. As complex and demanding as these design challenges have been, it is safe to assume from recent history, more are to come.