From Composite Risers to Subsea Drilling Rigs New Technology Driving Ultra-Deepwater Drilling
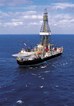
Houston, Texas
Contents
Deepwater drilling activity is viewed by some as the glamorous side of the offshore oil and gas industry. While wells in several thousand feet of water were drilled in the 1970s, it has not been until the past four to five years that deepwater exploration has really taken off. Because of the long lead times of exploration, development, and production of deepwater fields, this segment of the business has been less affected by low oil prices than E&P in the shallower areas.
From the beginning of 1996 until mid-1999, 237 wells were drilled in water depths of 3,000 ft or greater. This includes 46 wells (19%) in greater than 5,000 ft of water. Sixteen wells were drilled in water depths between 6,000 ft and 6,999 ft while five were drilled in water depths greater than 7,000 ft.
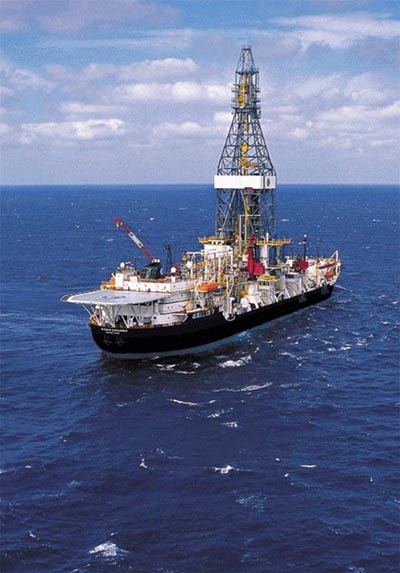
A record water depth well in 8,022 ft is presently being drilled by Noble Drilling's semisubmersible Paul Wolff for Petrobras off Brazil, exceeding the previous record by more than 300 ft That well was drilled by Global Marine's drillship Glomar Explorer in the Gulf of Mexico in 7,718 ft of water, and remains the Gulf of Mexico water depth record holder. The three other wells drilled in excess of 7,000 ft of water also were drilled in the US Gulf of Mexico by Shell, Marathon, and Elf.
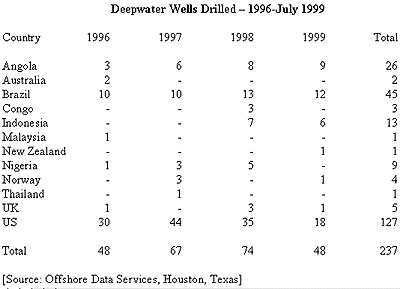
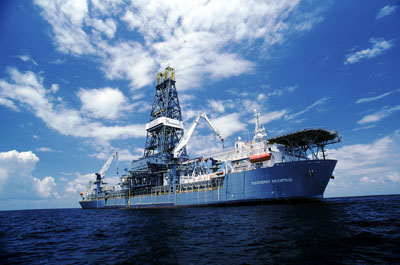
Several drillships have been delivered from shipyards that are designed to drill in 10,000 ft of water. Additional drillships and semisubmersibles rated to drill in 8,000-10,000 ft of water are presently under construction. Because of their sheer size and the complexity of state-of-the-art equipment, these rigs are estimated to cost US$300-400 million each.
Evolving technologies and new concepts could result in smaller semisubmersibles and drillships becoming capable of drilling in water depths of 8,000-10,000 ft and deeper. These include lightweight composite risers, titanium risers, riserless drilling, subsea mud lift systems, and a futuristic concept for a subsea drilling rig.
Composite materials reduce weight (back to top)
ABB Vetco Gray has been developing a composite marine drilling riser for the past 2½-3 years and presently is preparing to field test a single composite drilling riser joint in a conventional steel riser string for three months. This test is scheduled to take place on a Pretrobras well off Brazil during the first quarter 2000. The composite riser joint will be placed in three different locations of the string to achieve different load regimes.
The key to composite riser technology is connecting a metallic end fitting, or connection, to the composite tubing. ABB Vetco Gray has patented Geometric Trap technology whereby the metallic end fittings are mechanically mated to the composite body tubes of the riser joint. This, according to the company, results in reliable connections because the preload stress in the joint region eliminates relative motion and is not affected by the harsh service loading a riser normally experiences. Composite drilling risers can reduce overall riser system weight by more than half.
ABB Vetco Gray manufactured composite choke and kill lines that are less than half the weight of steel lines. The company also completed a design for a 10¾-in. production riser and is currently manufacturing three joints for in-house testing. They hope to field test the production riser joints around the same time as the drilling riser, although they are still soliciting partnerships for that test.
The cost of composite material risers is a factor in addition to the acceptance by the industry of this new technology. "Composite material risers are never going to be cost-effective," according to Gary Galle with ABB Vetco Gray. "Where you save is in the overall system. If you have a drilling riser that is good for 5,000 ft of water, a composite riser can save up to 60% of the weight and that same vessel can go into much deeper water. So do you build a whole new vessel or do you buy a composite riser?"
"Acceptance of the technology has gotten a lot better," Galle said, "but it is difficult to convince the industry that it will be an economic winner for them. That is more of the focus now."
Cameron has considered the concept of composite materials for drilling and production risers for some time but has focused on other alternatives because of concern during inspections, among other things.
"We are very impressed with the structural properties of composites," said Bill Taylor, Manager of R&D for Cameron in Houston. "However, there are some daunting problems that still exist, in our opinion. One of them is the pragmatic issue regarding inspection during the service life. It is very difficult to spot a joint made of composite that needs replacing. That particular issue worries us a lot."
"The integrity of the bond between the composite structure and the metal end connection over time is what needs to be confirmed," said Pat Holley, Director of R&D for Cameron.
"This industry is geared for steel," Taylor said, "and I don't think that could be overstated. I think the industry will hang on to a steel solution as long is it makes sense. We may be reaching a point in the next few years where it will be examined again, but we believe there are other non-steel alternatives that are in the running. Titanium is one of them."
Cameron supplied the first titanium production riser for Conoco's Heidrun Field in the North Sea several years ago.
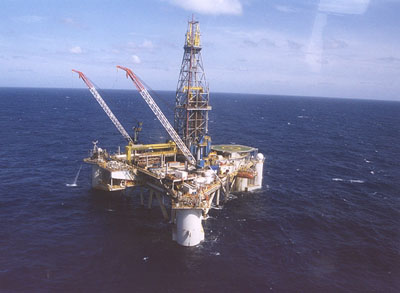
Riserless Drilling Concepts (back to top)
DeepVision, a joint venture of Transocean Offshore and Baker Hughes, was formed in 1998 to research, develop, and implement new drilling technologies utilizing larger diameter coiled tubing for riserless drilling applications in deep and ultra-deepwater. An initial phase completed during 1998 included a study of the technical and commercial feasibility of continuous reeled pipe in combination with a dual density mud concept for deepwater drilling.
Phase two, presently underway, is focused on developing the equipment and technologies for deepwater drilling using reeled pipe. A possible third phase could begin before the end of this year with the objective of introducing a new approach to ultra-deepwater drilling.
ABB Vetco Gray has been chosen by DeepVision to develop a composite material mud return riser system. This would be a separate riser returning the mud and cuttings to the surface.
Conoco several years ago formed a joint industry project (JIP) to initially examine the riserless drilling concept, while also studying alternative deepwater systems. As the JIP progressed, the riserless concept, although still under study, gave way to the SubSea MudLift Drilling system, a dual gradient drilling technology. Presently the industry utilizes a single gradient drilling system to control bottom hole pressure via a mud column extending from the bottom of the well to the rig. A dual gradient system controls the same pressure through a combination of mud from the bottom of the well to the mudline, and only seawater in the riser from the mudline to the rig.
A main benefit of the SubSea MudLift Drilling system, and a primary goal of the riserless system as well, is that several casing strings can be eliminated. With the mud in the riser replaced with seawater, less riser tension is required, thus extending the water depth capabilities of smaller rigs.
"The riser is not much of a limitation once you take the mud out of it," said Ken Smith, JIP Project Manager with Conoco. "The big problem with deepwater risers is that the mass they contain is so huge that they cannot stand so much of the environmental loads anymore. We use the drilling riser basically as a seawater-filled conduit for the drill pipe and a carrier for the BOP control lines and the mud lift system."
With a riserless drilling system, the concept theoretically allows exploration in limitless water depths. With the use of a drilling riser and the SubSea MudLift Drilling system, there could be a constraint on the applicable water depths "but I don't know where that would be," Smith said. "We certainly are capable of drilling with the mud lift system and the marine riser filled with seawater anywhere in the Gulf of Mexico, which I think bottoms out at 11,000 or 12,000 feet of water."
"We are seeing so much improvement in the ability of the marine riser to go farther once we take the mud out of it and replace it with seawater," Smith said, "that taking this out to 12,000 or 14,000 ft of water really is not going to be a problem for the big rigs."
The four-phase JIP anticipates commerciality of the SubSea MudLift Drilling system perhaps during 2002 following the manufacture of a full system in 2001 and testing the following year.
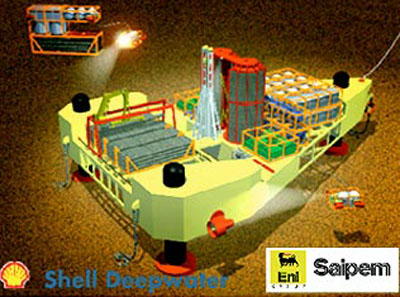
Shell International Deepwater Services (SIDS) and Saipem have joined for the past two years on the concept of a subsea drilling system, which could be the ultimate riserless drilling system. The drilling system looks like a submerged jackup-shaped drilling rig. The companies say if the requirement for a riser can be avoided then it should be, and one way to do that is to place the entire drilling system on the seabed.
The rig would be constructed using fixed foam buoyancy incorporated within the structure to make it slightly negatively buoyant. The unit would be lowered to the seabed with a lift line from a surface support vessel and once on the seabed and leveled the control umbilical would be connected by an ROV.
The subsea drilling system would be controlled via the umbilical from a dedicated surface vessel that would provide electrical power and control, compressed air for buoyancy and possibly some liquids such as cement or additives. All of the critical systems will have redundancy in case of a failure.
The drilling package would be a fully automated marinized system similar to those installed on the latest state-of-the-art deepwater rigs. The drilling package probably would utilize a hydraulic derrick. Pipe would be handled in single joints stored in vertical racks. The bottom hole assemblies would be standardized as much as possible and be stored in a second rack similar to that for standard drill pipe.
An operator on the surface vessel would control the rig. While the controls on the subsea drilling rig itself would allow for semi-automatic operation, in the early phase of the operation a driller would be in charge of controlling the subsea rig with joysticks and a computer interface. To enhance the situation for the driller, real time video, sound, and possibly even vibration would be fed back to the driller.
SIDS and Saipem estimate the cost to build such a subsea drilling system would be approximately $471 million. This cost, according to the companies, includes a significant amount for designing and building the initial unit, and subsequent rigs would be significantly cheaper than the first unit.