GE's New Pressure Sensor Is First With New TERPS Technology
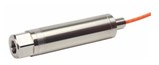
Offers High Accuracy, Stability and Flexibility
GE's Trench Etched Resonant Pressure (TERPS) technology is now available for the first time in a range of new pressure sensors from the Sensing business of GE Energy, Measurement & Control Solutions. The RPS 8000 and the DPS 8000 resonant silicon pressure sensors offer accuracy and stability greater by a factor of ten over existing piezoresistive pressure sensors and significantly extend the pressure range capability conventionally associated with resonating pressure technology (RPT) sensors. The new sensors feature physical isolation from the pressure medium through a metallic isolation diaphragm and an oil-filled chamber and this enables a very robust packaging, suitable for harsh environments. A wide selection of electrical and pressure connectors is available to suit specific requirements. Typical applications range from aerospace to sub-sea and from process engineering and metrology to industrial instrumentation.
As Ian Abbott, product manager for pressure sensors, explains, "Through our Druck product line, we have been able to offer a resonant silicon product, the RPT Series, for some years. The new TERPS technology is the result of extensive research and development into the design and manufacture of silicon resonating pressure sensors both within GE and in collaboration with Universities. The RPS 8000 and DPS 8000 sensors incorporate this technology and feature all the inherent features of resonant silicon, but with significantly greater capability in terms of pressure range (up to 70 bar), temperature range (-40°C to +85°C) and mechanical packaging. In addition, the bulk micromachining of the silicon, a technology we have migrated from our Advanced Sensors business, greatly improves product delivery dates."
The new sensors operate in essentially the same way as an RPT sensor. The silicon structure is driven into resonance by the application of an electrostatic field and when pressure is applied to a diaphragm, the silicon resonator is stretched, changing the frequency, much like a guitar string. This change in frequency relates directly to the applied pressure. The RPS 8000 and the DPS 8000 sensors differ only in their respective outputs. The DPS 8000 incorporates an integral microprocessor and RS485/RS232 outputs to provide direct digital output. The RPS 8000 delivers a TTL frequency output and a mV temperature measurement from an integral temperature diode. These can be combined in a customer's own digital equipment to provide a pressure reading. The RPS 8000 is ideal for OEMs and systems developers who wish to incorporate high accuracy, stable pressure measurement.
The TERPS technology employed by the new sensors uses three major manufacturing and packaging techniques. Deep reactive ion etching allows the creation of complex and arbitrary geometries within the resonating structure. This optimizes the design and performance of the resonator to make higher pressure and temperature ranges possible. The use of silicon fusion bonding allows for the machining of separate components of the sensor to be processed separately and then fused together retaining the properties of single crystal silicon. This provides greater flexibility in the design of the sensor element making higher pressure and temperature ranges possible. A new frequency detection method that provides a much stronger signal from the resonator, has made it possible to package the sensor element in a way that can be mechanically isolated from the process media. This is a significant advancement for a sensor of this performance class over other high accuracy technologies that are typically limited to dry non-corrosive gases. In addition, associated electronics can be further from a TERPS sensor, which permits operation in higher temperature environments.
About Measurement & Control
Measurement & Control is a leading innovator in advanced, sensor-based measurement, non-destructive testing and inspection and condition monitoring. Providing healthcare for our customers' most critical assets, we deliver accuracy, productivity and safety to a wide range of industries, including oil & gas, power generation, aerospace, metals and transportation. Measurement & Control has over 40 facilities in 25 countries and is part of GE Oil & Gas. For more information, visit www.ge-mcs.com.
About GE
GE works on things that matter. The best people and the best technologies taking on the toughest challenges. Finding solutions in energy, health and home, transportation and finance. Building, powering, moving and curing the world. Not just imagining. Doing. GE works. For more information, visit www.ge.com.
GE Energy works connecting people and ideas everywhere to create advanced technologies for powering a cleaner, more productive world. With more than 100,000 employees in over 100 countries, our diverse portfolio of product and service solutions and deep industry expertise help our customers solve their challenges locally. We serve the energy sector with technologies in such areas as natural gas, oil, coal and nuclear energy; wind, solar, biogas and water processing; energy management; and grid modernization. We also offer integrated solutions to serve energy- and water-intensive industries such as mining, metals, marine, petrochemical, food & beverage and unconventional fuels.
SOURCE: GE