Inclination-at-the-Bit Sensor Reducing Tortuosity, SWD for Real-time Seismic Measurement Making Geosteering More Reliable
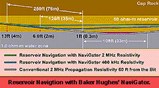
Houston
Over the past decade, directional drilling has led to efficiencies that have helped drop recovery costs in some areas, including the Gulf of Mexico, from as much as $15 per barrel to less than $3 per barrel. Most of these high-angle wells are drilled with positive displacement motors (PDM), known as mud motors in combination with angled subassemblies that push against the formation to force the bit in some desired direction.
But the advent of 3D seismic processing has pressed engineers to do more than merely build or drop the well bore angle. Armed with their new weapon, geophysicists are now able to pick smaller targets with greater confidence that they are indeed hydrocarbon-bearing sands. And, by stringing together several of these small targets with a single well bore, once uneconomic pockets of reserves can be made profitable.
The theory was fine but the practice of making multiple directional changes and maintaining constant wellbore direction for extended sections was cumbersome. In order to affect the required numerous inclination and direction changes it was necessary to stop drilling, pull out of the hole, change the BHA and trip back in to resume drilling. Likewise, keeping tabs on bit location was done through electric wireline measurements that again forced a temporary halt to drilling. Such rig down time is particularly galling offshore where daily costs routinely run from $60,000 to $250,000. Too, once drilling is stopped, particularly in high angle wells, any number of things can happen down hole, including catastrophic well bore collapse.
Industry responded by first giving operators the ability to locate the BHA without coming out of the hole. That soon evolved, over more than a decade, from simple measurement while drilling (MWD) to logging while drilling (LWD). This ability to locate the bit was soon coupled with the means to change the angle of the bent sub from the surface while drilling. The practice is known as geosteering.
While their prototypes have been around since the mid-1980s, drilling engineers only became sufficiently confident in (MWD) tool measurements to forgo confirming electric log runs in the mid-1990s. The addition of a gamma ray tool to MWD made it possible to locate the bit geologically and the addition of induction and density neutron tools soon gave engineers an even greater sense of security.
Today, operators can get the same information while drilling, including the longtime standard suite of logs known as the triple-combo - density lithology, neutron porosity and induction - that once required expensive, time-consuming log runs over the section of interest. This information not only takes engineers beyond mere LWD to formation evaluation in real time (FEWD), it allows them to actually locate the bit in an earth cube rather than simply in relation to offset well logs or geologists' predictions.

While geosteering was a tremendous breakthrough for directional drilling, nothing is perfect, and in the few short years it has been practical, it has evolved immensely. In its earliest incarnation for example, the sensors feeding data to the surface were by necessity 30 ft - a full tool joint - behind the drill bit. And while that may not sound like much in a miles-long extended reach well, it did create some real problems.
For instance, since the bit was 30 ft passed the spot being measured, drillers often found that some unexpected change in the formation being drilled - either softer or harder, for example - had caused the bit to rise or drop precipitously. Correcting the problem, forcing it either up or down, particularly when done several times over a section of well, created small hills and valleys along the well bore.
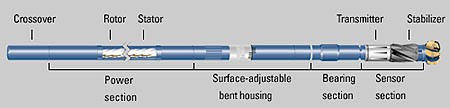
The severity of the resulting ripples, their number and angle, is called wellbore tortuosity. Tortuosity can cause difficulties later in trying to install tubulars in holes with close casing-to-wellbore diameter tolerances. Also, it has been shown recently that in open hole completions, water can settle in the low sections of these peaks and valleys and act to choke production.
The obvious answer to smoothing out the wellbore was to place the sensors at the bit. But two hurdles made such an innovation difficult. At the bit there is simply not enough room for the sensors and signaling equipment. And the environment at the bit is so harsh that few sophisticated sensors can survive the pounding.
For now, while most of LWD tools remain a safe distance behind the bit, service companies are perfecting tools and systems to at least measure inclination at the bit (IAB). While locating the IAB sensor itself at the bit was mainly a matter of building a tool robust enough to last in such a punishing environment, space restrictions still made it impossible to place the mud pulse signal generator there.
The solution to that physical restraint has been to leave the mud signal generator 30ft behind the bit. The IAB is then programmed to send its data signal into the formation through which it travels back 30 ft to a sensor that translates it to a mud pulse to be relayed to the surface. As a result, the angle of the bit is known in real time.
While the near bit inclination sensor solves the gross problem of tortuosity, still some exists since corrections are still made only after the bit has achieved a wrong angle. In some sections, such as when a bit follows a fault that forces it to head up or down, corrections are being made constantly.
That is because communication and data systems in geosteering tools are essentially one-way. In other words, no confirming signal is sent from the bent sub to tell the driller it has made the requested angle change. Observers on the surface can only be sure the proper turn has been made when the LWD tools well behind the bit signal back their location.
The most promising approach to dealing with that problem may be the "closed-loop" system. Under such a scheme, the signal from the IAB tool at the bit would be processed instantly by a computer and any slight change in angle, or any indication of a tendency to deviate from a pre-programmed direction would be adjusted even as it was starting. The result would be direction changes too small to create the kind of problems associated with tortuosity.
The latest addition to the suite of logs available in LWD format is the sonic tool. It was, as can be imagined of a tool that relies on sound to take measurements, the most difficult to place near a bit that is crunching formation while fluids rush by carrying debris to the surface.
Having solved the problem of sound interference chiefly through electronic filters, the advent of the sonic while drilling tool has made a reality of something drilling experts have thought theoretically possible but perhaps pragmatically too complex to accomplish - seismic while drilling. The sonic tool was for some time the last ingredient to that effort as without it calibrating real-time readouts to seismic measurements could be done only indirectly at best, the sonic leg of the system being essentially an implied one.
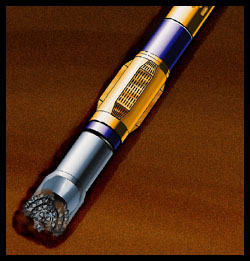
The next step for geosteering and its associated sensors and tools that record and report the world around the bottom hole assembly is a system to see ahead of the bit. While only in the conceptual stages at the moment, such a system would interpret the geophysical markers some distance ahead of the bit and enable the operator (or the computer since it will almost certainly be a closed loop system) to make direction changes accordingly. The result would be a smoother, more efficient well bore void of unnecessary dog legs.
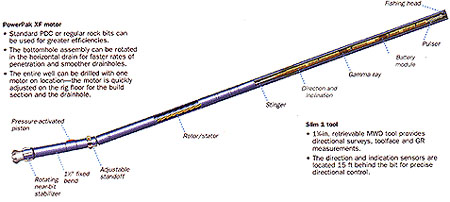
The ability to steer the bit and gather data essential to efficient completions all while drilling has been a boon to both major oil companies and smaller independents. In areas that have long been deemed uneconomic by large companies, smaller operators are making good returns on their investments by tapping small but numerous pockets of hydrocarbons left behind by their huge competitors.
And because of the huge investments involved in deep water projects, major oil companies are demanding maximum production per unit of infrastructure. That can only be accomplished through longer and ever more accurate, reaches from each platform.
It can easily be argued, then, that geosteering is a technology second only perhaps to 3D seismic in its affects on the current health of the upstream oil and gas industry.