New Calcium Chloride & Polymer Drilling Fluids Suited to Deepwater & Friendly to Environment
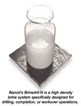
by John Murphy, Houston
Drilling fluids professionals today, particularly in today's exploration and production offshore hot spots, live with the forces of two environments. The first and most familiar to them is that of the world beneath the earth's surface, where pressure, temperature and rock characteristics determine which mud will render the fastest, most in-gage and ultimately most productive well.
But in today's oil industry, the environment above ground in terms of what will render the most healthy planet, is on a par with those old parameters as a driving force behind fluids innovations. In the North Sea for instance, discharging any drilling fluids, even those with no hydrocarbon content, will be forbidden. Most industry insiders believe it is a policy that will spread.
"The UK is making discharge of any kind illegal and the US probably soon will," said MI's Bob McLarty. "We will see a day when we can't use synthetics because of the discharge question."
That the relatively new synthetics-based muds are on their way out is ironic. They were designed to replace oil base mud (OBM) systems that use hydrocarbons as the base fluid, with a synthetic base that uses bases created in the lab. They are environmentally friendly, as is water-based mud (WBM), but provide such OBM-benefits as lubricity and a way to drill water-sensitive formations without causing them to swell and slough into the wellbore.
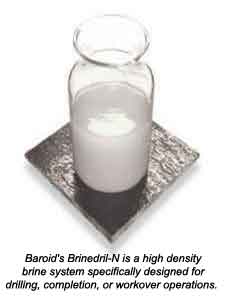
Of course, modern rigs are equipped to drill without discharging anything to the sea and often do once the top section is drilled with returns to the seabed. But in today's oil industry, even a remote chance of spilling hydrocarbons into the environment is deemed unacceptable, especially if any measure exists, no matter how inconvenient or costly, that could prevent such a gamble.
One answer, according to McLarty, is to alter water-based systems to include some of the desired SBM and OBM characteristics of hole-cleaning efficiency, lubricity, and inhibition (prevention of shale swelling in water-sensitive formations). His company produces a system marketed under the name CALDRIL that uses calcium chloride (CaCl2) and polymers.
"The recent goal has been a water based mud good for deep water environment," he said. "I think we have gotten there. The problem [in deepwater] is such things as emergency riser disconnect or a riser break. We do not want oil-based mud flowing into the sea [during those events]."
The combination of salt (CaCl2) and polymer provides the water system sufficient viscosity to carry cuttings to the surface while the CaCl2 prevents swelling of water sensitive clays.
Baroid Technical Manager, Gary West, says his company has made another breakthrough by creating a fluids system incorporating calcium chloride and calcium bromide to duplicate the benefits of SBM. "It gives good rheological properties with good shear qualities and viscosifying capabilities you don't often get in brines," he said. "It has low solids, good inhibition, and lubricity. It can even suspend barites. This has never been available before with a heavy brine."
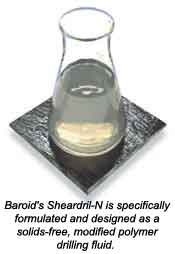
Beyond being a threat to the environment, engineers have long had another complaint against OBM that MI claims to have in hand for those instances when such a fluid is still the optimal choice. "Oil based muds restrict the quality of electric logging tools," said McLarty. "Bad electric logs have been a problem forever. MI has developed a fluid that uses an additive to allow conductivity."
The new downhole environment has also forced drilling fluids experts to create new products, known generally as "drill-in" fluids. They are designed to meet the special demands created by drilling long horizontal sections through productive zones.
"Drill-in fluids are designed to keep the formation in check and for easy cleanup," said McLarty. "It especially must be easy to clean when using pre-packed sand screens."
Cleaning up means removing the filter cake from the wellbore wall. (Filter cake is residue left behind by mud being deposited on the wall as the bit passes.) It is desirable while drilling, as it keeps the wellbore in tact, but is not when it coats the production zone and stymies flow. When screens are used to prevent sand flowing into the well with the gas and oil, clean up is especially important as a filter cake can flow into the screen and choke all production.
Still, unless the well is to be drilled underbalanced, a filter cake is an unavoidable and necessary evil. To gain the benefits of a filter cake while assuring minimum damage, drill-in fluids often exhibit two characteristics: they are clean, that as few solids as is required to gain the necessary density to control formation pressure; and they are easily removed from the wellbore wall.
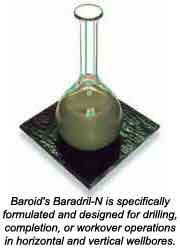
While occasionally a well is drilled with a perfectly clean fluid, one that has no solids at all, in most instances the heavy particles used in traditional muds to plug pore spaces (and create filter cake) are replaced in drill-in fluids with polymers. They are smaller and lighter than barites or other traditional weighting materials. The fluids therefore also contain salts to act as "bridging" agents to partially fill the largest pore spaces upon which the small polymers can build a barrier across the exposed pore throat.
Polymers for these specialty fluids are also chosen for their acid solubility, that is, how easily they will dissolve when rinsed with acid. Once a long section is drilled, the sooner the completion team can clean the hole the less chance for formation damage. If the polymer is not dissolved quickly in a single acid bath, for instance, the mud can continue to invade the formation and hinder accurate log interpretation, cement placement, and production.
Not all polymers fit all situations and the explosion in high-angle drilling has created a varied list from which to choose the proper drill-in fluid. "Everyone has lookalikes," said McLarty.
"We have seven drill-in fluids and we look at the application and pick one that fits the particular situation," West said. "Then we custom fit [that choice] to the reservoir characteristics of the well in question."