New Equipment, Methods Key to Greater Advances in Underbalanced Drilling
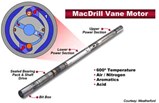
by John Murphy, Houston
Until recently, with very few exceptions, wells were drilled overbalanced. Drilling fluids were designed with a density such that their resulting hydrostatic pressure at the bit would be greater than the pore pressure of the formation being drilled. The idea was simple—force high-pressure gas, water, and oil in the formation to remain in place using higher pressures.
It evolved over the years as an answer to the wasteful practice of old in which drillers simply blundered into the zones of interest, allowing oil and gas to roar to the surface. The resulting geyser was dramatic but outrageously wasteful, environmentally irresponsible, and extremely dangerous. But while drilling overbalanced made more sense, it also had its drawbacks. Dense drilling fluids can do more than contain the formation. As drilling engineers have long known, muds whose density's have been raised by the addition of solids can also damage a well's ability to produce when those solids separate from the fluid, invade the formation, and plug the pore throats through which oil and gas must flow to the wellbore.
In certain circumstances, this fluid damage can reduce a well's productivity to a point it becomes uneconomical. With the proliferation of extended-reach drilling and the practice of reentering depleted zones to wring the last bit of hydrocarbon from a mature formation, engineers were faced with the dilemma of practicing prudent well control while not damaging the low-pressure formations through fluid invasion.
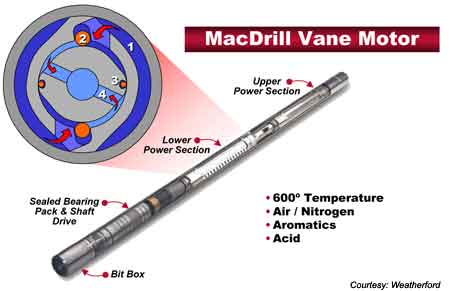
Increasingly, the answer to the problem has been underbalanced drilling (UBD). It is a practice based on a goal diametrically opposed to that of traditional drilling operations that seek to contain any movement of well fluids to the wellbore. While drilling underbalanced, using a fluid whose density is less than that of the pore pressure equivalent density, well fluids are allowed to flow to the surface even as the formation is being drilled. The outward flow prevents drilling fluids' solids from entering the rock's porous surface.
"This is especially true in horizontal wellbores," said Houston consultant Don Warlick of Warlick International. "Your objective is to expose as much of the pay zone as possible but using heavy drilling fluids you go against your objectives. Ultimately you want to reduce formation damage and that is an area that only in recent years has been given the attention it deserves."
While controlled underbalanced drilling, including air drilling that uses no drilling fluids, has been practiced on a small scale for more than 40 years, interest in modern underbalanced drilling techniques coincides with the proliferation of horizontal drilling. As operators began to hone their ability to drill increasingly longer stretches through pay zones formations they turned to UBD as the method to do so without damaging them.
But lately, others have been touting the science for its ability to improve drilling performance. "On average, though the data is still not in, you get rates of penetration (ROP) of about two times that of overbalanced drilling," Warlick said. "Essentially when you have a regular mud column, you are holding down the chips on the formation face, but if you lighten up the fluid, the chips fly off the rock face and the bit has a new face to drill."
"A good majority of our revenue comes from deeper, cheaper with fewer drilling problems," said Ted Wilkes, a manager in Weatherford's newly organized, 400-member underbalanced drilling team. "If you can drill twice as fast while only adding 10-15% to the overall costs there is a lot of savings there. There is also a lot of value in directional work because you have a lot of people on location and a lot of equipment and if you can do it faster the savings are easy to see. So we do a lot of reservoir lateral drilling for [improved] ROP with the secondary objective being formation damage [prevention]."
There are other financial rewards to the practice not initially considered by pioneers of modern UBD. "You set up additional equipment to take flow as you are drilling and you can tap that early production and do production tests while drilling," Warlick said. "Then there is no need for conducting expensive testing and the more important feature is you can take early production. On some smaller wells that can make the difference in the economics of the thing."
And since the formation was presumably left uncontaminated by drilling fluids, there is presumably no need to stimulate the well, eliminating another significant new well expense. "In the end you drilled it faster and left it in an enhanced state," Warlick said. "The only economic negative, if you can call it a negative, is that you may have spent a little extra money for wellsite recovery and you have been a little more careful on safety precautions."
Ironically, though drilling a well while it flows hydrocarbons intuitively seems a more dangerous proposition than traditional methods, preliminary as yet unpublished statistics suggest otherwise. The Texas Railroad Commission has reportedly used well control incidents as a measure to gather data indicating UBD to be 30-35% safer. Wilkes says that because of UBD procedures he can believe such numbers.
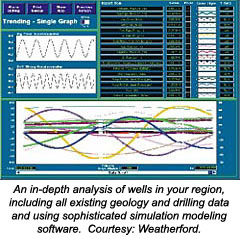
"In conventional fields, sometimes you have done it a lot and your guard is down," he said. "With underbalance you really have a lot of eyes on the instrumentation and you are ready to handle a kick."
Contributing to UBD's good safety record and growing acceptance among operators as a way to drill faster even in normally pressured formations is the track record of equipment recently developed especially for the procedure.
The most significant of these innovations is undoubtedly the rotating blowout preventor (RBOP), field-tested and perfected primarily in Texas's Austin Chalk formation by Williams Co., now a part of Weatherford, in the early 1990s. The RBOP is able to maintain a pressure seal between drill pipe and casing even as the drill string is turning. Hydrocarbons returning through the casing annulus are diverted by the RBOP to a flow line.
A choke upstream of the RBOP is also used to control the well flow and in consequence the pressure on the formation below. By opening the choke, the well flows more easily and the back pressure against the formation is reduced. Conversely closing the choke increases back pressure on the zone being drilled as it slows flow.
Several methods are used to lower the density of the drilling fluids. It can simply be a fluid mixed at a density less than the equivalent pore pressure or, particularly in zones of very low pressure, nitrogen or some other gas of a specific gravity less than water can be entrained in the fluid, thus lowering its density significantly.
But the latter option can create problems of their own, particularly when drilling a directional well with a mud motor. Mud motors turn the bit via positive displacement using fluid flow across steel vanes housed in rubber inner-housings, or stators. When drilling underbalanced, the fluid used often contains hydrocarbon-based solvents or gases that can corrode the rubber stator.
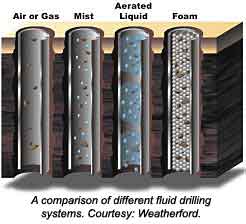
In response companies have developed mud motors with stainless steel stators that not only resist corrosion but operate in 600°F and can remain in the well even during acid treatments that would destroy rubber stators.
That section of the well that must be drilled underbalanced is often completed with a simple slotted liner cemented only at the top. It is a procedure that grew out of the need to keep costs down and is sufficient as few of these wells are drilled beyond the zone in question.
However simple and economical such a completion strategy may be, it is not well suited to extended reach sections with multiple zones of interest that might be better served by isolation. Unfortunately, the best isolation practices require a cement sheath and precisely placed perforations. And cementing in low-pressure zones faces presents the same fluid invasion problems as does traditional heavy drilling fluid and can actually fracture the reservoir and drain away, making a good cement bond impossible.
To meet this challenge (as well as several others having to do with offshore operations) cementing companies have designed what has become known commonly as foamed cement. It is made lighter by injecting Nitrogen into the cement slurry as it is being pumped down the hole. It has the attraction of a very low density but can be perforated and once set up holds pressure as well as traditional primary cements.
It is difficult to tell how the industry is taking to UBD. According to Wilkes, one study sponsored jointly by several major service companies, reports operator 2000 budgets call for about 9.5% of their wells to be drilled underbalanced—a significant number.
But the study, says Wilkes, pointed up something else that he finds more troubling. He calls it an educational gap among operators. "When asked more specific questions (by the surveyor), the response was often no comment because they didn't know what he was talking about," Wilkes said. "There is gaping hole in people's knowledge. They know about it and think it is cool but don't really understand it."
Toward the end of closing such a gap and standardizing practices, definitions, and terminology, the International Association of Drilling Contractors has formed a subcommittee on underbalanced drilling.