Not A Drop Of Oil Lost: How Modern Clamp-On Technology Contributes To A Reliable And Cost-Efficient Pipeline Management
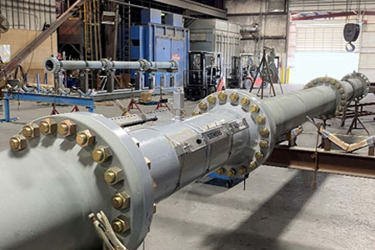
Transporting crude oil and petroleum products through pipelines is currently the most efficient way to distribute these energy sources to their respective destinations. To protect the environment and against loss in value due to leakage or theft, systems for leakage detection are required. To ensure safe operation, pipeline management systems must be continuously adapted to the state of the art. Modern and improved ultrasonic clamp-on flow meters offer cost-effective options at this point.
State-of-the-art for pipeline measurements
Typically, ultrasonic inline measuring instruments are used in pipelines. The sensors are installed asymmetrically in pipe segments, several pairs of sensors determine the flow profile and flow speed by measurement, from which the volume flow is determined. Very long straight inlet sections ensure a balanced flow profile, and this is exactly how the system is calibrated externally.
Ultrasonic clamp-on measuring instruments do not achieve this measurement accuracy. Mounting the sensors directly on the pipeline pipe does not permit a comparable calibration. Clamp-on ultrasonic signals are transmitted exclusively through the center of the pipe, so a metrological flow profile determination is not possible. And in practice, flow profile deviations due to non-ideal inlet conditions are often unavoidable.
Different products in pipelines pose another challenge. Different media densities cause changes in the refraction angle of the sensor signal irradiation into the pipe. This changes the ideal receiving position of the sensors and, in extreme cases, the signal drops out of the receiving range in large pipes.
Clamp-on holds a lot of potential for cost-efficient pipeline management
The typical measuring principle of ultrasonic flow measurements works according to the propagation time difference method. In terms of measurement, only the two signal propagation times and the time difference in both directions are measured. The signal propagation time enables a conclusion to be drawn about the current acoustic velocity of a liquid; the time difference is proportional to the flow velocity.
This is where the calculation tasks for the measuring instrument commence. The current flow volume is determined based on the pipe dimension and flow velocity as well as the Reynolds number, which describes the current flow profile. The Reynolds number is continuously calculated in the measuring instrument based on viscosity at the current temperature, flow velocity, pipe dimension, and roughness of the pipe wall. To monitor a 50-km-long segment, a balance calculation is required, which takes into account the different process conditions of the input and output measurement. For this purpose, a back calculation to a comparable standard volume is carried out in each measuring instrument.
There are convincing reasons in favor of clamp-on measuring instruments for monitoring pipelines that cannot be denied:
- High absolute measurement accuracy, very high relative measurement accuracy due to identical segment monitoring
- Non-contact measurement technology, no contact with hazardous products
- Retrofitting possible at any time, maintenance periods or system shutdown is not necessary
- No production downtime in the event of a defective measurement, simple sensor replacement
- Active measurement even during pig operation for any required pipe cleaning and pipe diagnostics, even detection and reporting of a pig run through
- Product or batch detection by measuring the acoustic velocity
- No moving parts, no wear (also applies to inline)
- No need for external calibrations
- Self-monitoring through equal measurement path weight (acoustic velocity and zero flow)
- Significantly cost-effective way to improve safety in existing plants
- Galvanic isolation (cathodic protection concept) and lightning protection
- Low investment risk, try and buy
Partnering with customers to meet the requirements of the industry
These arguments have motivated Siemens to find ways to improve this technology. For more than 20 years, we have had a partnership with a pipeline operator for continuous technical development. The new SITRANS FS230 system is field-proven and now satisfactorily monitors the entire pipeline network.
The project, supervised by the German Technical Inspectorate (TÜV), aimed to equip a DN1000 pipeline over a length of more than 600 km with better and more accurate clamp-on measurements and to integrate them into the existing pipeline management system for leakage detection. The accuracy of the clamp-on measuring units was verified against existing calibrated turbine-type meters. Demonstrably, the measurement deviation was less than 1% under almost all operating conditions. This resulted in possible savings, to replace the calibrated turbine-type meters and avoid recurring costs.
The clamp-on measuring instruments provide all measured data for process control with sufficient absolute accuracy. The balancing of sectors for leak detection takes place with a higher relative measuring accuracy, since all devices have the same conditions compared to each other.
So how can SIEMENS improve pipeline safety with the new SITRANS FS230 Flowmeter?
SITRANS FSS200 clamp-on sensors are the basic prerequisite for high measurement accuracy. Signal transmission is harmonic according to the Lamb wave principle, the signal frequency is precisely adapted to each measuring point. Each sensor size covers a specific wall thickness range. The exact operating frequency is automatically determined optimally during first commissioning each time. The sensors are operated in reflective mode. The WideBeam method ensures that crude oil mixtures with both high and low density are still within the safe reception range of the measurement signals.
Almost all measuring points have been changed to the 4-path method. Especially in the event of retrofits, ideal inlet conditions are almost never found. A high number of sensor pairs at one measuring point improves the measurement accuracy, anomalies in the flow profile are detected more easily.
The sensors are fixed via stainless steel enclosures, which are firmly attached to the pipe and can even withstand earthquakes. If the sensors are mounted in ducts, this ensures uniform temperature conditions without direct solar radiation, resulting in longer maintenance intervals.
However, the key to accurate measurements is the new SITRANS FST030. This transmitter consists of a basic device and an external Digital Sensor Link (DSL). The innovative idea behind this is the separation of the analog sensor electronics from the transmitter and thus an extremely short distance to the sensors.
The electronic module in the DSL housing handles the entire analog measured value signal as well as the subsequent digitalization of all data. Temperature and pressure, which are necessary for the volume calculation, are recorded externally via analog inputs. Data exchange and power supply of the DSL are handled by an SSL cable (Siemens Sensor Link). Digital data is thus reliably transmitted over distances of up to 150 m. Sensors and DSL can be used in Zone 0/1, the transmitter depending on the version and housing type are also Zone 1 or 2. Short analog sensor cables to the DSL decisively improve EMC (Electromagnetic compatibility) safety and additionally save costs.
Complex task: Handling multi-product pipeline measurements
Up to four pairs of sensors can be connected to one DSL, enabling accurate flow profile measurement. Thanks to a signal rate of 100 Hz, very fast signal processing is achieved even with 4-path measurements. Each path provides 25 measured values per second. This dynamic response improves the accuracy of measurement and, incidentally, lays the foundation for reliable pig detection, even with short overall length and high flow velocity.
For pipelines with different products or batches, products are detected by measuring the acoustic velocity. All product variants are stored in a Liquident (liquid identification) table. Thus, a liquid is detected and assigned taking into account the current temperature under reference conditions. The stored data is used to calculate the current volume flow, taking into account the current viscosity, i.e., a Reynolds-number-based flow profile determination. A back calculation to standard volume or density calculation is then very easy.
Defined API standard products such as diesel, gasoline or liquefied natural gas (LNG) are predefined and stored in the measuring device. For different crude oil blends, the table is adapted to the customer's specific requirements. Here you look at all the mixtures used and divide them into up to 30 different liquids. Each table entry is given a name and a range of possible acoustic velocity at standard conditions, e.g., 15.6°C and 1 bar. Other stored values are density, standard volume, viscosity, and temperature properties.
Transporting different batches of crude oil through a pipeline requires longer-term customer-specific adaptations. The experience of our specialists is helpful during initial commissioning and subsequent fine adjustments. Of course, it is also possible and useful to improve clamp-on measurement accuracy by calibrating against highly accurate existing built-in measurement units. All these measures lead to impressive results.
Since it can be easily retrofitted, the clamp-on method allows segments to be extended, or it can be used to add another check measurement with high reliability in critical sections. Test measurements can also be applied quickly and without risk at any time.