Smart well technology split between hydraulics-based systems & all-electric systems
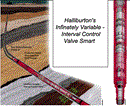
By John Murphy, Houston
Despite a great deal of talk about their near-revolutionary ability to increase oil and gas production efficiencies, smart wells, or intelligent completions, have made little headway toward widespread acceptance since the first one was run in the North Sea in 1997. That, say observers, is because they are caught in a Catch-22 of sorts.
The idea behind smart well technology is to stave off costly intervention for routine maintenance such as production logging and planned operations to shut off one zone and open another to production once the primary zone is depleted. As such, an indispensable characteristic of smart wells is reliability. After all, a failure that would require a workover or abandonment of the well would defeat the purpose of a smart well altogether.
Industry experts say a smart well system should be reliable for at least five years and in areas such as deep and ultradeep water where intervention is extremely costly, they expect assurance downhole sensors and devices will work for ten years. So as operators at once demand smart wells prove their reliability and remain reluctant to be among the first to put the expensive intelligent completions in their wells, the technology has had little chance to prove itself and so has evolved only slowly despite its early promise.
Still, while smart well development has progressed slowly, it has not stopped. Many service companies, led by the big four of Baker, Schlumberger, Weatherford, and Halliburton, all are moving forward to perfect both the downhole devices that will make up smart wells and the systems to run them. And as they have done so, two basic schools of thought are emerging as to what bases the technology should take. One camp, owing in some measure to the conservative nature of the upstream oil industry, supports hydraulics-based systems. The other favors all electric systems and is further divided into subsets in favor of and opposed to the use of fiber optics downhole.
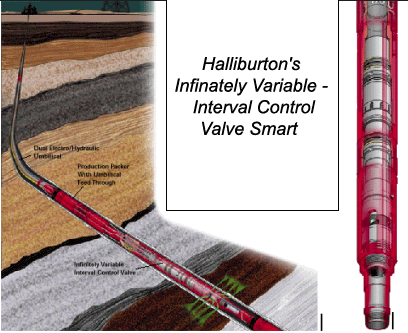
Perhaps predicting this debate, the system widely recognized as the first true smart well installation and done by a small firm of innovative engineers working in the UK North Sea, comprised a sliding sleeve that moved vertically within the production string to open, shut-off, or regulate the volume of flow from a particular zone. The sliding sleeve, a direct descendent of the venerable wireline-activated sliding sleeve, was actually an electro-hydraulic hybrid. It employed electronic signals to activate a hydraulic motor that in turn moved a sleeve across open ports in the production string.
Today, the majority of operators weighing in on the debate remain in favor of hydraulic systems. They are, they say, simpler because they have fewer moving parts and since the oil industry has a history using hydraulics, it is more comfortable with them. Those same factors also make hydraulics a less expensive choice while their track record elsewhere in the industry also fosters a perception of proven reliability.
Despite this industry bias, electronics advocates believe it is a matter of time before their systems become the norm in smart well installations. Electronics, they argue, are more easily deployed and will certainly prove more reliable over time. Indeed, electronics are even now proving their reliability in wells where they are being used in permanent downhole temperature and pressure gauges and in some instances for downhole flow measurement.
The technology that advocates say will finally spur the industry towards smart well development is the coming proliferation of offshore multilateral wells. Using adjustable chokes to regulate flow from each lateral as an overall reservoir production strategy or to regulate flow in each lateral where many zones may be flowing to a single production string will demand sophisticated control and numerous zone shut offs and openings.
"In these long laterals, production tends to come from the heel rather than the toe of the lateral," explained Paul Tubel, until recently head of intelligent completions at Weatherford, now president of Tubel Technologies. "That means production comes from the deeper zones and when water hits at the deepest zone the only alternative is to shut in the whole branch."
In other words, once the deepest zone begins to see water, production from the whole branch will be lost as water will dominate the production train unless the individual zones can be isolated so as to shut off watered out zones and open others further up the lateral. But the cost of carrying out such an operation with a deepwater rig can be sufficiently high to make a very strong negative impact on some properties and to actually kill the economics of marginal ones.
Therefore smart wells can be designed so that the deepest zone can be shut off remotely and others further up the completion opened. In some instances, it may be necessary to not close a zone completely, but only to reduce its flow rate sufficiently to allow production from lesser-pressured ones to enter the wellbore. Finding the exact setting to achieve a desired flow rate for each lateral would be nearly impossible with standard wireline tools as would be measuring pressure and temperature readings with sufficient accuracy to determine what amount of production any one zone was contributing to the overall lateral flow. Again, this can be done quickly and cheaply with remotely controlled sliding sleeves and permanent downhole sensors.
"In the past it was not known where the [production] water was coming from," Tubel said. "Pressure and temperature monitoring combined with flow control from the surface makes intelligent completions a perfect solution for that problem. Once the sensors indicate water has hit, the operator can shut in one zone and turn on the other. Then the whole lateral can be produced."
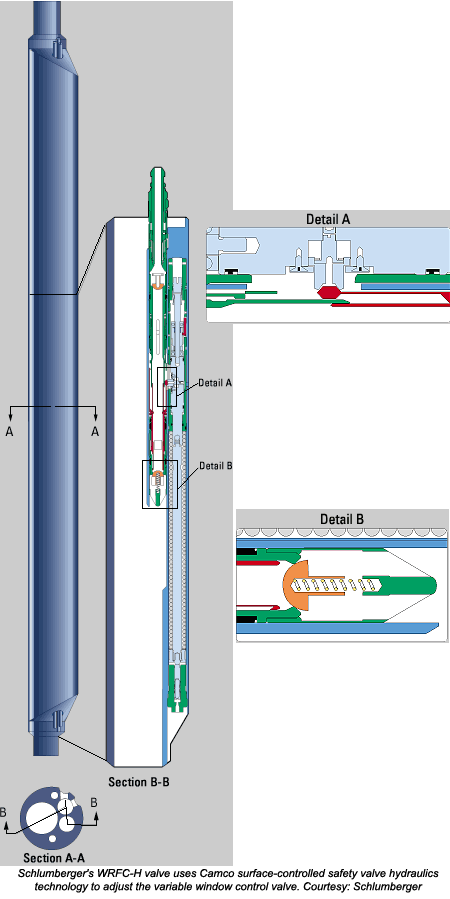
The final image of intelligent wells as first presented to industry was as a self-regulating, ultra efficient production method. In its most sophisticated form it was envisioned that the smart well would monitor and send parameters such as temperature, flow rate and pressure throughout the completion to a computer at the surface. The computer would then compare production against a model of the most efficient production scheme. The system would then adjust the flow control devices to ensure maximum production efficiency while at the same time continually updating the original reservoir and production models.
But, says Tubel, that concept is some ways from reality. "We are now nowhere near that concept in the field," he said. "Customers in this industry are very conservative and for now they are looking only for the very low end technology. [Operators] tend to say ‘why should I put a costly system in my well that could easily cause me problems?' It will get there but not any time soon."
Such an attitude is likely to change with the proliferation of multilateral technology in deepwater. Indeed, one leader of smart well technology development is rumored to be on the verge of installing an all-electric smart well system for giant BP on one of its deepwater Gulf of Mexico fields. And Total has plans to install smart well sensors – one a source and one a receiver in an offset well – to create real time, cross-well tomography that will allow them to monitor fluid movement in the reservoir. "It has the advantage [over traditional tomography] in that it is permanently in place," said one service company designer assigned to the project. "Besides having continuous data in real time, you also never have to worry about [sensor and source] locations being different from one reading to the next."
When smart wells will becomes fully accepted as a completion option is still open to debate. "I think we are only beginning to understand what is required so I think we are a ways off," said Schlumberger VP David Malone while discussing the future of smart wells late last year. "Before this becomes common practice it is going to be like horizontal drilling once was and take about ten years to develop. It will come in stages depending on how complex the environment is."
The horizontal well analogy is one commonly heard throughout the industry. That technique was perfected not because it was an interesting option but because it had real applications with real financial drivers in the prolific Austin Chalk play that demanded extended reach sections drilled through narrow pay zones. The same can be expected of smart well technology. When the risk of installing exotic remote controllers and sensors is overshadowed by the extreme costs of workovers in a sufficient number of deepwater developments, demand for smart well technology will surge. And ten years from now seems about right.