Technology pushing drilling beyond 10,000 ft water depth
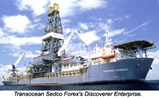
By Jerry Greenberg, Houston
Contents
Risers for 10,000 ft of water
Dual gradient mud lift systems
Rig shortage could be looming
Ultra deepwater rigs
Drilling riser technology is the key to successful ultra deepwater exploration, say equipment manufacturers, but several drilling contractors believe the industry has the capability to drill in 12,000 ft of water and greater with current technology. Several of the newest offshore drilling rigs are designed for 10,000 ft of water or greater, while others can be made capable of those water depths with a few modifications such as additional drilling riser and more and larger riser tensioners. A primary concern is the ability of the formation to withstand pressures from the weight of mud in the drilling riser system. Consequently, two joint industry projects and at least one operator are developing dual gradient drilling systems for virtually limitless water depths.
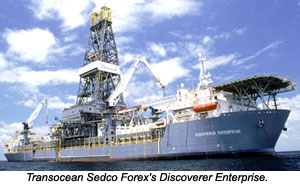
Risers for 10,000 ft of water(Return to Contents)
Lightweight drilling risers for ultra deepwater are being developed. Noble Drilling, for example, is developing an aluminum alloy riser. ABB Vetco Gray is working on a composite riser about 60% lighter than one of steel. Both companies hope to test prototype riser joints in the field in the first quarter 2001. Additionally, Stewart & Stevenson has introduced the first dual gradient riser that utilizes composite material for the auxiliary lines.
ABB Vetco Gray has been developing its composite riser for several years and plans to field test a joint in a well being drilled by Petrobras early next year. A concern with composite risers was the interface with the metal connector, which Vetco Gray solved with a patented technology whereby the metallic end fittings are mechanically mated to the composite body tubes of the riser joint.
While the composite riser is only 40% the weight of a steel riser, there still may be the need for buoyancy material, particularly at the top of the string. And there may also be a section of steel joints at the bottom of the string to provide of extra weight when the riser is run from the rig to aid the dynamics of the riser.
Composites are expensive, and ABB Vetco Gray's system is no exception. "Our goal is to be somewhere between 2 and 2 ½ times the cost of a steel system," said Gary Galle, their manager of composites and floating production systems. "I don't know if that limits the market. Whenever you use composites, you are generally in 5,000 ft of water and beyond. Often, economically, composites come out way ahead when you consider the total system costs of buoyancy, vessel, and variable deck weight."
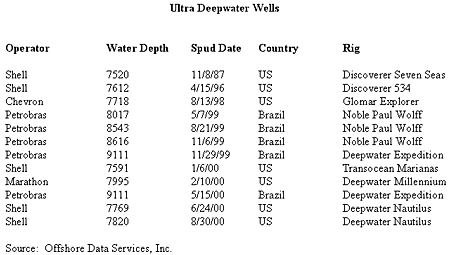
One of the advantages, Galle says, is when the riser is returned to the rig and stored on deck, the variable weight is much less than a steel riser. "You definitely can use a smaller rig," he said. "And the ironic thing is that these riserless drilling systems offer some of the best opportunities for composite risers because the riser can be much lighter and smaller."
Anticipating development and eventual commercial availability of dual gradient drilling systems, Stewart & Stevenson introduced the first riser system designed specifically for that application. The company says its riser will work with any of the three dual gradient drilling system concepts currently under development. The riser's somewhat cumbersome name, Dual Gradient Drilling Mud Return Marine Riser System (DMRS), doesn't get in the way of the simplicity of the design. All of the dual gradient concepts utilize a line to return mud and cuttings to the surface. The DMRS integrates a fifth, 7.4-in. ID mud return line and a riser isolation tool into the riser.
The riser is heavier and more expensive than a typical steel riser, but Stewart & Stevenson is offsetting some of the additional weight with composite materials for the auxiliary lines. This is also where much of the higher cost is involved. It can be used in up to 12,000 ft of water.
The riser is available now. Among its advantages are less drilling fluid requirements achieved by decreasing the amount of fluid in the riser by two thirds; reduced tension requirements due to the reduced fluid within the riser; higher return fluid velocities; and continuous flow over the shakers.
Dual gradient mud lift systems(Return to Contents)
Three concepts of the dual gradient mud lift system for ultra deepwater drilling are underway, including one joint industry project (JIP) aimed at field testing by year-end. Each is designed to allow drilling in extreme water depths and minimize or remove the possibility of formation damage resulting from the large hydrostatic head above the well. Essentially, offshore wells could be designed the same as a land well.
The Conoco/Hydril JIP has been developing its SubSea MudLift Drilling system since October 1996 and is in the process of manufacturing and fabricating a complete system for testing in the US Gulf of Mexico during the first quarter 2001 on a Texaco well with Diamond Offshore's semisubmersible Ocean New Era. Water depth will be approximately 1,150 ft of water.
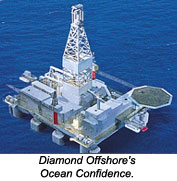
"The only difference between 1,150 ft of water and 11,000 ft as far as our system is concerned, is the length of pipe that brings the seawater down and the length of conduit that brings the mud back up," said Ken Smith, JIP project manager with Conoco. "There is no technology there, only pipe. So it's a perfectly valid, accurate test of the system."
The concept was originally dubbed riserless because each of the three concepts originally sought to eliminate the drilling riser, but they realized there still needed to be a conduit from the surface to the well. The Conoco/Hydril mud lift system requires an additional line for mud return. "Our system as well as the others requires additional lines," Smith said. "Stewart & Stevenson came up with a neat way of devising an additional line but it is not necessary."
"We have come up with ways to modify an existing riser on the rigs we use so we can get the lines in place as well," Smith continued. "It would really depend on whether you are looking at a newly built riser or you have one you are willing to modify."
DeepVision, the Transocean Sedco Forex, Baker Hughes, BP, and Chevron JIP, was begun in 1997, and hopes to have a commercial product by the end of 2002 or early 2003. It is intended for the Gulf of Mexico initially, for use in 4,000-7,000 ft of water with the capability for 10,000 ft with minor modifications.
A third dual gradient drilling system being developed is Shell E&P Company's subsea pumping system (SSPS). The concept can be configured to fit various vessels, be moored or dynamically positioned. The company says a riserless configuration is also possible, in which only the return conduit is used and the drillstring and casing are deployed through open water.
Rig shortage could be looming(Return to Contents)
Ultra deepwater rigs are those capable of drilling in 7,500 ft or more of water. There are currently 17 rigs rated (equipped) for those water depths with another dozen under construction, according to Offshore Data Services (ODS). [Rated water depth here means the rig is capable of drilling in those depths, regardless of whether it may be designed to drill in 10,000 ft of water or more.] A few more rigs could possibly be upgraded to fit this depth category.
Interestingly, although 17 rigs can drill in ultra deepwater, only two were actually drilling in those water depths at the beginning of October, one in 7,600 ft of water off Brazil and another in 7,800 ft of water in the US Gulf of Mexico.
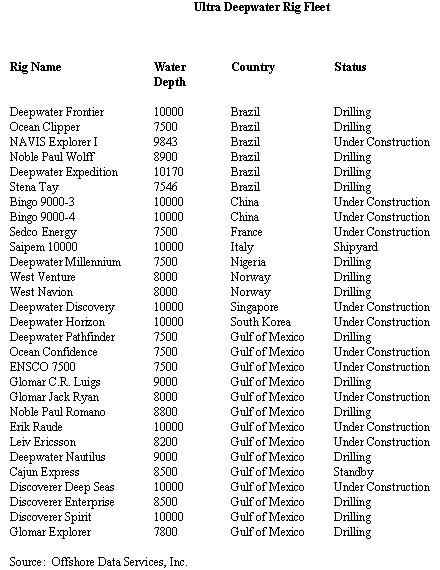
By early to mid-2001, all of the present new construction of ultra deepwater rigs will have been delivered. All but two are contracted, the Bingo 9000 designs owned by Ocean Rig under construction in China. Their hulls have been fabricated but a decision to outfit them as drilling rigs or production units has not been made.
But despite the number of ultra deepwater rigs, at least one analyst believes the industry faces a shortage by the end of 2001 due to increasing energy demand.
"Over the course of the next 12-24 months," said Tom Marsh, drilling analyst with ODS, "the drilling market is going to tighten considerably, likely toward the end of that time frame. We are probably looking at a shortage of deepwater rigs in 2002 at the latest."
Marsh also says there will be additional new construction anticipating this rig shortage. "There are three hulls that are presently not being outfitted, and I would think those would wind up as drilling units," Marsh said. "There are still a few hulls that could be upgraded into that depth, but we are forecasting the need for additional capacity, and the only way to get it is probably new construction."
Ultra deepwater rigs(Return to Contents)
While several of the newest rigs are designed to drill in 10,000-12,000 ft of water, only a few are equipped to actually work in 10,000 ft. Most are equipped for 7,500-8,000 ft. The depth capability depends almost entirely on the amount of riser aboard the rig, but increasing the capability to 10,000 or 12,000 ft may be relatively simple.
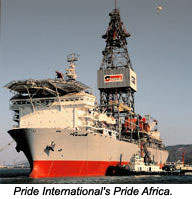
"Basically going to deeper waters would be accomplished by a simple addition of risers and probably changing the subsea accumulator bottles on the BOP," said Thomas Duhen, technical director at Pride International in Houston. Two of the company's new drillships, Pride Africa and Pride Angola, are designed for 10,000 ft but are presently equipped for 6,000 ft. Duhen says the rigs would need little else other than additional riser, since they are already structurally designed and built for operation in 10,000 ft.
That is essentially the same situation with the recently delivered drillships Glomar C.R. Luigs and Glomar Jack Ryan. They are designed for drilling in 12,000 ft of water but are presently equipped for 9,000 ft and 8,000 ft. Basically all that would be required to enable the rigs to operate in 12,000 ft would be additional riser and adding two tensioners to the eight already installed on the rig due to the heavier riser.
"Technology can take us to 13,000 or 14,000 ft if necessary," said Marion Woolie, President of Global Marine Drilling. "The technology utilized to get to 12,000 ft can be used to get to 13,000 to 14,000 ft if required."