The Unstoppable Growth Of Reinforced Thermoplastic Pipes
By Yash Pathak
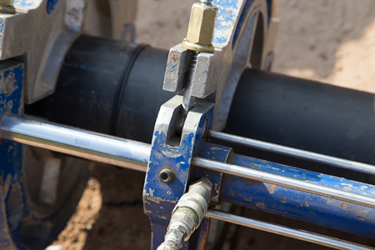
The need for non-corrosive alternatives to conventional pressure conduits has given birth to reinforced thermoplastic pipes. Rapid deployment of reinforced thermoplastic pipes counters the inherent drawback of steel pipes: corrosion, weight, and fatigue. Major end-use industries such as oil and gas were among the first ones to venture into reinforced thermoplastic pipe applications in large-scale manufacturing processes. Reinforcement materials such as aramid and polyester make reinforced thermoplastic pipes perform efficiently under extreme conditions. These products have been recognized by the American Petroleum Institute (API) as an ideal alternative for the flowline point of application by major operators of the oil and gas sector. The combined strength of thermoplastic liner, helically wrapped continuous fiber reinforcement, and external thermoplastic jacket is a primary factor for this recognition.
Reinforced thermoplastic pipes do not show any signs of discoloring, fraying, breaks, cuts, buckling, and reorientation, even after years of continuous use. Oil and exploration projects across the world have been a major growth lever for reinforced thermoplastic pipe manufacturers. Countries such as the U.S. have been multiplying their shale gas production further increasing the demand for reinforced thermoplastic pipes. Similar developments in Gulf countries such as UAE, Saudi Arabia, and Qatar will also contribute to the surging demand for reinforced thermoplastic pipes in the coming years. Manufacturers of oil and gas products will continue to propel the demand for reinforced thermoplastic pipes on the back of low maintenance cost and longer product lifecycles.
COVID-19 Disrupts Demand Growth In Near-term
The supply and demand imbalance due to travel restrictions and industrial slow-down, particularly in the chemicals industry, has a direct impact on reinforced thermoplastic pipe manufacturers. Unprecedented supply shock and demand drop continues to be a major concern for oil and gas manufacturers. The sector’s worsening financial health will most likely force budget-costs and business-model alterations. Excessive supply of shale gas and petrochemical products further increase the burden on the limited revenue pools. As prices touch 30-year lows and social distancing reduces the recurring demand from consumers, oil and gas operators face a major revenue generation challenge.
The COVID-19 pandemic has accelerated one of the most transformative moments in the oil and gas industry. These factors and their impact on the value chain of oil and gas products will filter down to reinforced thermoplastic pipe manufacturers in the form of diminished demand for their products. Companies are witnessing order cancellations and quantity revisions across end-use industries. Investor scepticism and increasing public and government pressure regarding the environmental impact of industrial manufacturing adds to the difficulties of reinforced thermoplastic manufacturers. The competition in coming years will be driven by technology-led rapid supply chain changes to capture the flat to declining demand for reinforced thermoplastic pipes.
Reinforced Thermoplastic Pipes Pave Way For Cost Savings For Consumers
Reinforced thermoplastic pipes are bringing in profits for their customers. Their utilization reduces the annual expenditure on anti-corrosion measures. The global annual expenditure to mitigate corrosion is around US$2.5 trillion, according to the National Association of Corrosion Engineers, a globally recognised body for anti-corrosion measures. Prevalent methods to fight corrosion such as water injection is a temporary solution as it leads to sourer hydrocarbons and therefore speeds up the corrosion rate overtime. Reinforced thermoplastic pipes are anti-corrosive by nature, they can withstand harsh environments and high-pressure fluid exposure. This has been the most important growth lever for reinforced thermoplastic pipe manufacturers. The applications of this product are versatile in nature. It can be deployed in flowlines, risers, jumpers, and expansion spools for uses such as chemical and methanol injection, gas lift, wellbore access, choke and kill, and decommissioning and intervention of steel pipe infrastructure.
The ability of reinforced thermoplastic pipes to be customized as per customer specific environments makes this a profitable alternative to steel pipes. Melt-fusing manufacturing processes ensure a true composite internal structure and enhance the interface bond between different pipe layers. The challenging offshore and subsea environments require a thermoplastic matrix that fully embeds fibers within the polymer matrix. The fibers hence produced are liners and do not deform or decay in the long run. Reinforced thermoplastic pipes are based on this technology and hence continue to produce cost savings and enhanced performance for its customers. These pipes are lighter than their metallic equivalents and can be installed in smaller vessels. The value proposition of reinforced thermoplastic pipes is two-fold: first, it completely eliminates the huge anti-corrosive costs; and second, it reduces the installation costs considerably. Reinforced thermoplastic pipes reduce expenditure by 35 percent as compared to conventional metallic pipe installation.
Pipeline Innovations To Accelerate Revenue Growth
Tech-driven advancements in molecular science and manufacturing processes cement reinforced thermoplastic pipes as a dependable option when it comes to withstanding high-pressure end-uses. Reinforced thermoplastic pipes are competitive from 10 to 20 km end-use against steel pipes. In case of corrosion resistant alloys, reinforced thermoplastic pipes fare better than alloys in costs, production capabilities, and product customization. A few notable advancements that drive reinforced thermoplastic pipe adoption are:
- Infusion with polyamide 12 (PA12) that can withstand up to 10,000 psi (689 bar) and 80℃ (180℉) in water injection use-cases.
- Carbon fiber produced with polyvinylidene difluoride (PVDF) qualifies to withstand a pressure of 10,000 psi and 121℃ (250℉).
- Weight coating that stabilizes pipe installation on seabeds, eliminating the need for concrete, ropes, or chains.
- Integration of optical fiber and sensors to regularly monitor pipeline integrity and leakages.
- Enhanced insulation for high-temperature applications.
These are a few of the many advancements in reinforced thermoplastic pipe manufacturing that have increased the demand for this type of pipelines. The relatively low maintenance cost, coupled with greater customization options, present a lucrative opportunity for customers and generates gainful prospects for manufacturers of reinforced thermoplastic pipes.
Future Of Global Reinforced Thermoplastic Pipe Market
Industrial automation in manufacturing processes will emerge as the leading competitive business strategy. Major market players in the reinforced thermoplastic pipes market are investing in capacity expansion strategies to capture significant market value share. North America has been a leading region in revenue generation over the past years. The reinforced thermoplastic pipes market in North America was valued at US$81 million in 2019. However, the Middle East and Africa (MEA) will surpass North America by 2030. MEA will account for more than one third of the total market value expanding at an annual compounded growth rate of 6 percent between 2020 and 2030. MEA is a leader in terms of oil and gas production facilities. The proliferation of construction projects to enhance the oil and gas production will generate remunerative opportunities for reinforced thermoplastic pipe manufacturers. The market competition is highly consolidated with top ten players accounting for more than half of the total market value. Key stakeholders in this market are, but not limited to, Baker and Hughes, Cosmoplast, H.A.T-Flex, National Oilwell Varco, OPR Offshore Pipelines & Risers Inc., PES.TEC, Saudi Arabian Amiantit Co., Saudi Aramco, Shawcor, and Wienerberger AG.
Yash Pathak is a research consultant at Fact.MR, with a proven experience in market research and consulting industry and has been closely working on Chemicals & Materials vertical of Fact.MR. Yash is instrumental in developing strategies and providing consultancy at Fact.MR, as well as holds expertise in providing Go-No-Go decision recommendations, plant feasibility studies, route to market, long-term production capacity and utilization planning, demand projections, sensitivity and plant location analysis, and price benchmarking, among other key skills. Insights presented in the articles are based on the findings of Fact.MR’s ongoing extensive research on Reinforced Thermoplastic Pipes Market.