Seeq Corporation
1301 2nd Avenue Suite 2850
Seattle, WA 98101 US
Seattle, WA 98101 US
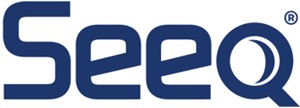
Company Overview
Seeq® enables process manufacturing organizations to rapidly investigate and share insights from data in historians, IIoT platforms, and database web services as well as contextual data in manufacturing and business systems.