Technical progress allowing subsea production with less risk & cost
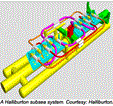
By John Murphy, Houston
Contents
Saving space & costs
Subsea oil-water separation
Systems seafloor bound
As operators venture farther from shore into increasingly deeper water, certain parameters of only minimal concern on land or on the continental shelves have become critical. Deep water, and to an even larger degree ultradeep water beyond about 7,500 ft, create physical isolation that forces operators to have close at hand as much of the equipment necessary to maintain operations as is physically possible. That in turn makes deck space a premium on offshore facilities, called host platforms, designed to process subsea well production before it is sent ashore.
As subsea xmas trees have become less expensive to build and install and, at least to some extent, standardized, the industry has begun to perceive them as increasingly reliable. At the same time, special tools and vessels that have been developed for the purpose have made intervention considerably less costly. As a result, subsea installations are proliferating.
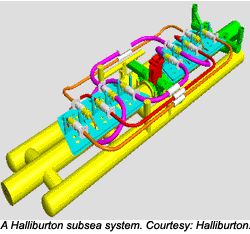
The upshot of this technical progress is to allow operators to develop fields once thought too small to support either the risk of subsea completions or the costs of dry trees with floating facilities. Still, subsea completions face challenges, prominent among which are those associated with water production and the associated headaches brought on by flow assurance problems and the need to dedicate large amounts of deck space to processing equipment.
Also, a subsea completion is often not an option in deepwater frontier areas when discoveries are made far from any existing host platforms or other infrastructure. In such cases, as Shell, BP, and others have famously demonstrated in the US Gulf of Mexico, the operators must sink millions, sometimes billions, of dollars into building immense floating tension leg platforms and spars.
Saving space & costs(Return to Contents)
As part of their efforts to address these problems, engineers are developing a number of space and cost-saving technologies. The most popular approach being simultaneously undertaken by the likes of Framo and ABB in Norway and the Brown & Root division of Halliburton in the US among others is to bring normally surface-based processes off the platform and onto the seabed.
Nearly all systems traditionally based on the surface appear fair game for removal to the ocean floor. Separation, testing, pipeline pumping, and gas compression are all on the drawing board or actually available for installation on the seabed. But in order for these solutions to be successful they must prove themselves beyond mere functionality: they must make economic sense and, since intervention is still costly for such complex systems, they must be virtually maintenance-free.
Subsea oil-water separation(Return to Contents)
Subsea oil-water separation has gained a great deal of attention throughout the offshore industry. And the reasons for the interest are obvious. Reliable sources estimate the oil and gas industry worldwide produces about seven bbl of water for every bbl of oil. And while many old, depleting onshore fields contribute the lion's share of that ratio, water handling offshore costs the industry a great deal more money per bbl of produced oil than it does on land—it is simply more complicated and therefore more expensive to process and dispose of produced water at sea, the deck space needed to house separators, piping, and disposal systems adds greatly to the capital costs of the facility itself.
In 1999, ABB delivered what it touted as the world's first subsea and separation and injection system in 350-ft waters off the coast of Norway for Norsk Hydro and in June, pronounced the installation fully operational. The system, Subsis (subsea separation and injection system), can be monitored and controlled remotely and is designed to inject water separated from the oil-water stream directly back into the reservoir.
The company, besides laying claim to the first such installation, also owns some specific enabling subsea technologies and estimates the market for subsea separation at about US$500 to $600 million, primarily in the Gulf of Mexico, the North Sea, and off West Africa.
"The first Subsis installed was a little more expensive, of course, simply because it was the first," said ABB vice president Chris Barton. "But we have priced several out since then and they will be commercial at about $25 million to $30 million."
Since subsea systems re-inject separated water back into the well, concerns about flow assurance and risks to the environment are also greatly reduced since there is no water in the flowstream to initiate hydrate formation or to be discharged into the sea.
"Operators are really interested in the flow assurance aspect," Barton said. "If you knock out the water early hydrates have no chance to form. It is a perfect solution to a very serious problem for deepwater production."
While at the moment water is simply injected in a disposal systems, it is likely in the future the water will be re-injected into the producing zone to maintain formation pressure and eventually enhance recovery. This could eliminate the extreme costs of building injection systems should the operator opt for a secondary water flood recovery later in the life of the field.
"It is not really for production enhancement yet," said Barton. "At the moment the water is contaminated and we simply dispose of it. We will need a fine filter system to get rid of the solids in the water before it can be re-injected into the producing formation. But we are looking at that concept with an added filtration system."
But perhaps the most important effect of removing water at the seabed is that its effect can also be to greatly increase ultimate recovery. That is because by reducing the volume of fluid that must be lifted by formation pressure to the surface or along long sea bottom pipelines, back pressure against the producing zone is greatly reduced.
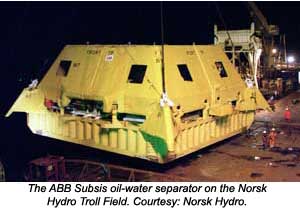
"We can enhance recovery by up to as much as 50% by reducing back pressure," Barton said. "Abandonment pressure is lowered which improves ultimate recovery and also improves oil and gas production rates since it is easier for the fluids to get through the reservoir, to the well bore and to the surface."
Finally, when water is removed at the seabed, smaller risers can bring more oil to the surface just as smaller pipelines and less pressure is required to move production along the ocean floor to the host platform. Reducing the cost and maintenance of infrastructure in turn reduces the field's economic limit, the point at which operating it equals the profits in oil and gas produced. In doing so many finds that might otherwise be adjudged marginal or uneconomic become profitable.
Systems seafloor bound(Return to Contents)
Other systems headed to the seafloor are in varying degrees of readiness. ABB is reported nearly ready to commercialize Sepdis, an electrical power distribution and control center located on the seabed to service the monitor and control devices on each of the often far flung subsea development components. The concept brings closer the complimentary technologies of subsea completions and smart wells as well as providing power closer to electrical components to reduce power losses along long cables leading to remote locations.
To provide testing capabilities subsea, Framo has developed a successful multiphase meter that unlike its competitors measures water, gas and oil directly rather than through complex calculations—a goal that has defied oil and gas industry efforts for years. Its ability to monitor and record flow rates for each phase of the flow stream without having to first separate them virtually eliminates the need for current production tests that must be done on a regular basis for accounting and regulatory purposes. It also clears large amounts of space on production platforms by removing separators, valve manifolds and test equipment and reduces production losses while the well is diverted to test separator for the duration of the test.
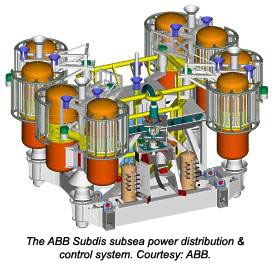
By rendering their multiphase flow meter suitable for subsea installation, Framo claims it can save operators space and money in other ways, too. By allowing operators to see in real time and constantly what their wells are producing, rather than intermittently only during scheduled test times, they can stave off problems before they occur.
For instance, rising water rates can indicate water is about to "break through" to the wellbore, cutting off the perforations from the reservoir. It is an event that often spells the end for producing wells once it happens but can be usually be delayed through intervention if the trend is spotted early on. Traditional tests are often done only monthly or biweekly, and by the time the rising rates are picked up in those tests it can easily be too late to do take effective corrective measures.
As operators come to understand the economic payoffs generated by moving surface equipment to the ocean floor, it is a strategy certain to become a major force in the development of the deep and ultradeep waters now in their sights.
For additional articles on subsea production, click on these links:
http://www.oilandgasonline.com/doc/showlegacy/A703AA7B-68C1-11D4-8C57-009027DE0829